Chapter
5 continued from...
Selecting an AQC
Acceptance Sampling and Testing
Plan |
 |
 |
Acceptance of the as-constructed pavement is based on the field
sampling of all of the included AQC's chosen by the agency. The PRS
approach ideally focuses on using in situ samples for acceptance, since
these samples provide a true indication of the properties of the
as-constructed pavement. Better estimates of the in situ quality will
ideally lead to better estimates of future pavement performance. Although
the current movement is toward in situ sampling, any agency-approved
sampling and testing methods may be utilized as long as they are performed
in accordance with one of the following standard specifications:
- American Association of State Highway and Transportation Officials,
Standard Specifications for Transportation Materials and Methods of
Sampling and Testing, Part II Tests.(19)
- American Society for Testing and Materials (ASTM), Annual Book of
ASTM Standards, Section 4, Construction, Road and Paving
Materials.(20)
An agency should, therefore, be able to implement the PRS prototype
approach without making major changes to its current sampling
methods.
There is also a current movement toward obtaining early
age AQC test results to provide the contractor with quick feedback
regarding the measured as-constructed pavement quality. Any test method
chosen for use in a PRS should ideally be timely, economical,
nondestructive, reliable, and reproducible. Although the current PRS
approach does not require the use of such early age testing methods, they
should be considered where appropriate.
Available
AQC Sampling and Testing Procedures
The following sections discuss the currently recommended AQC sampling
and testing methods and their use within the PRS approach. Until the
agency gains adequate experience with the current PRS approach and its
procedures, it is strongly recommended that the agency continue to use AQC
sampling and testing procedures with which it feels completely
comfortable.
Concrete Strength
Three of the distress
indicator models (transverse joint faulting, transverse fatigue cracking,
and transverse joint spalling) included in the current PRS approach
require concrete strength as an input. Specifically, these models require
a 28-day (equivalent laboratory maturity) flexural strength using a
third-point loading. Therefore, the agency must choose a sampling and
testing procedure that results in a direct measurement or indirect
estimation of this required 28-day flexural
strength.
Traditionally, the 28-day flexural strength has been
measured directly by conducting flexural strength testing on beams at 28
days of equivalent laboratory maturity. However, most agencies have
abandoned the practice of using beams for acceptance and have concentrated
on easier, more practical methods of estimating strength (such as 28-day
cylinder compressive strength). In addition, there has been a movement
toward accepting concrete strength based on early age (3-, 7-, or 14-day)
strength tests. The selection of a concrete strength sampling and testing
plan requires that the agency decide on a sampling type, the timing of
sampling, a test type, and the timing of testing. Some of the more typical
concrete strength sampling and testing choices available to an agency are
described in more detail below.
Sampling
Specimen Types for Concrete Strength
It is recommended that the sample concrete strength be measured using
beams, cylinders, or cores. If beams or cylinders are selected, these
samples are cast at the time of construction. If cores are selected, they
are to be extracted from the pavement at an agency-chosen time between 3
and 28 days of equivalent laboratory maturity. The details of each
sampling type are presented in the following sections.
Beams. Beam specimens (with agency-specified
dimensions) are to be molded, handled, and cured in accordance with
AASHTO T-23, Making and Curing Concrete Test Specimens in the
Field.(19) Beam specimens for each sublot are made with
plastic concrete taken from in front of or behind the paver at
predetermined random longitudinal sampling locations. Random
longitudinal sampling locations are identified in accordance with the
guidelines set forth in the section titled Selecting
a Random Longitudinal Sampling Location. The number of beam
specimens per sampling location (replicate specimens) and the number of
sampling locations per sublot are defined by the agency in accordance
with the guidelines set forth in the section titled Recommended
Number of AQC Samples Per Sublot.
Cylinders.
Cylinder specimens are molded, handled, and cured in accordance with
AASHTO T-23, Making and Curing Concrete Test Specimens in the
Field.(19) All cylinder specimens are cast in molds with
a nominal length-to-diameter ratio of 2. An appropriate cylinder
specimen diameter is determined based on the following:
- A minimum 102-mm cylinder diameter is used when the maximum
aggregate size is 32 mm or less.
- A minimum 152-mm cylinder diameter is used when the maximum
aggregate size is greater than 32 mm.
Cylinder specimens for each sublot are made with plastic concrete
taken from in front of or behind the paver at predetermined random
longitudinal sampling locations. Random longitudinal sampling locations
are determined in accordance with the guidelines set forth in the
section titled Selecting
a Random Longitudinal Sampling Location. The number of cylinder
specimens per sampling location (replicate specimens) and the number of
sampling locations per sublot are defined by the agency in accordance
with the guidelines set forth in the section titled Recommended
Number of AQC Samples Per Sublot.
Cores. Core
specimens are extracted from the hardened pavement slab between 48 and
72 hours after placement, in accordance with AASHTO T-24, Obtaining
and Testing Drilled Cores and Sawed Beams of
Concrete.(19) Core specimens are extracted from the
hardened concrete slab at predetermined random sampling locations.
Random sampling core locations are determined in accordance with the
guidelines set forth in the section titled Selecting
a Random Core Location. The number of core specimens per sublot
is defined by the agency in accordance with the guidelines set forth in
the section titled Recommended
Number of AQC Samples Per Sublot.
An appropriate core
specimen diameter is determined based on the following:
- A minimum 102-mm diameter is used when the maximum aggregate size
is 32 mm or less.
- A minimum 152-mm diameter is used when the maximum aggregate size
is greater than 32 mm.
Prior to testing, all core specimens are trimmed to a nominal
length-to-diameter ratio of 2.; A correction factor is applied (in
accordance with AASHTO T-24, Obtaining and Testing Drilled Cores and
Sawed Beams of Concrete) to cores having a length-to-diameter ratio
of less than 1.94, whereas cores having a length-to-diameter ratio
between 1.94 and 2.10 require no such correction.(19) Cores
with a length-to-diameter ratio exceeding 2.10 are reduced in length to
fall within the ratio limits of 1.94 to 2.10.
Timing of Concrete
Strength Testing
The agency must define the timing of the concrete strength specimen
testing to be used in estimating the 28-day (equivalent 28-day laboratory
maturity) flexural strength (third-point loading) of the as-constructed
pavement. Each specimen (molded beam, molded cylinder, or extracted core)
is tested independently and translated (if necessary) into an
MR at an equivalent 28-day laboratory maturity.
The
timing of concrete strength specimen testing is defined by the agency and
expressed in terms of an equivalent laboratory maturity. The agency-chosen
timing of concrete strength specimen testing must meet the following
requirements:
- Testing must not be conducted until the specimen achieves a maturity
of at least 72 hours (3 days) of the equivalent laboratory curing
condition maturity.
- Testing must be conducted at or before the point when the specimen
achieves a maturity equal to 672 hours (28 days) of the equivalent
laboratory curing condition maturity.
Testing-Related
Procedures (Conducted Prior to Specimen Testing)
The agency must perform the following testing-related laboratory and
field procedures (as required) in preparation for concrete strength
specimen testing.
Development of
Mix-Specific Maturity Curves
Prior to the placement of any as-constructed pavement, the agency must
develop required mix-specific maturity curves in the laboratory. The
representative maturity curves (expressed as flexural, compressive, or
split-tensile strength versus maturity) are determined using the Arrhenius
maturity method and in accordance with ASTM C-1074, Standard Practice
for Estimating Concrete Strength by the Maturity
Method.(20) The required developed maturity curves (and
corresponding equations) are included as Series A attachments to
the specification (see appendix A in this volume). This laboratory maturity
calibration is only required if sample testing is conducted when the
equivalent laboratory maturity is less than 28 days.
These
mix-specific strength to maturity relationships are determined prior to
construction by the testing laboratory contracted to develop the concrete
mixture design. The following procedure is used by the laboratory
personnel to develop these required relationships.
- Obtain adequate amounts of the coarse and fine aggregates, cement,
fly ash, and admixtures that will be used for the production of the
as-constructed concrete pavement.
- Cast a sufficient number of concrete beam and cylinder specimens in
the laboratory in accordance with AASHTO T-126, Making and Curing
Concrete Test Specimens in the Laboratory.(19) Note: It
is recommended that a minimum of 18 specimens be cast for each strength
type being investigated (i.e., 18 beams for flexural strength testing,
and 18 cylinders each for both compressive and split tensile strength
testing).
- Until the time of specimen testing, store the cast specimens under
standard laboratory curing conditions (in accordance with AASHTO T-126,
Making and Curing Concrete Test Specimens in the
Laboratory).(19) The maturity of the specimens should
also be measured over this curing period.
- Test the respective specimens at incremental ages of strength
development in accordance with the following AASHTO standards:
- Compressive strength of cylinders—AASHTO T-22, Compressive
Strength of Cylindrical Concrete
Specimens.(19)
- Split-tensile strength of cylinders—AASHTO T-198, Splitting
Tensile Strength of Cylindrical Concrete
Specimens.(19)
- Flexural strength (third-point loading) of beams—AASHTO T-97,
Flexural Strength of Concrete (Using Simple Beam With Third-Point
Loading).(19)
The number of testing ages should be sufficient to enable the user
to confidently predict strength from maturity. As a minimum, it is
recommended that three specimens be tested (for each strength type) at
equivalent laboratory maturities of 1, 3, 5, 7, 14, and 28
days.
- Plot the measured strength values (for each strength type) versus
the measured maturity values.
- Determine appropriate best-fit regression equations representing
each strength versus maturity relationship. The required developed
maturity curves (and corresponding equations) are included as Series
A attachments to the PRS (see appendix A in this volume).
Development
of Mix-Specific Inter-Strength Relationships
Prior to the placement of any as-constructed pavement, the agency must
also develop required mix-specific inter-strength relationships (i.e.,
compressive-to-flexural-strength, and/or split-tensile-to-flexural
strength relationships) in the laboratory. These specific inter-strength
relationships are determined by comparing the different 28-day maturity
strength values measured for the development of the appropriate maturity
curves. The required inter-strength relationships (curves and equations)
are included as Series B attachments to the PRS (see appendix A in this volume).
It is recommended that
the compressive-to-flexural-strength equation be assumed to have the
following form:
MR(28-day) = A *
(f'C(28-day)0.5)
(12)
where
MR(28-day) = Estimated flexural strength (third-point
loading) at a 28-day equivalent laboratory maturity,
MPa.
f'C(28-day) = Estimated compressive strength
at a 28-day equivalent laboratory maturity, MPa.
A =
Mix-specific coefficient determined through calibration using the means
of the measured compressive and flexural strength data at a 28-day
equivalent laboratory maturity.
The mix-specific coefficient (A) is determined using the computed
compressive and flexural strength 28-day maturity sample means (used in
the development of the maturity curves). Equation 12 is solved for A using
these computed sample means. Although the equation form shown in equation
12 is recommended, any agency-accepted equation relating compressive to
flexural strength may be used.
It is recommended that the
split-tensile-to-flexural-strength equation be assumed to have the
following form:
MR(28-day) = A *
(ST(28-day)/B)0.75
(13)
where
MR(28-day) = Estimated flexural strength (third-point
loading) at a 28-day equivalent laboratory maturity,
MPa.
ST(28-day) = Estimated split-tensile
strength at a 28-day equivalent laboratory maturity,
MPa.
A = Mix-specific coefficient determined through
calibration using the means of the measured compressive and flexural
strength data (at a 28-day equivalent laboratory maturity) in equation
12.
B = Mix-specific coefficient determined through
calibration using the means of the measured split-tensile and flexural
strength data (at a 28-day equivalent laboratory
maturity).
The mix-specific coefficient (B) is determined using the computed
split-tensile and flexural strength 28-day maturity sample means (used in
the development of the maturity curves). Equation 13 is solved for B, by
knowing A and using these computed sample means.
Specific
Concrete Strength Testing Procedures
Representative flexural strength (third-point loading) values at a
28-day equivalent laboratory maturity are determined for each specimen
using one of the following three testing procedures.
- Flexural Testing of Beams. If the concrete strength of the
as-constructed pavement is to be evaluated using beam specimens tested
in flexural strength (third-point loading), then the following procedure
is applied.
- Each beam specimen is tested (at an agency-defined equivalent
laboratory maturity) for flexural strength (third-point loading) in
accordance with AASHTO T-97, Flexural Strength of Concrete (Using
Simple Beam With Third-Point Loading).(19)
- Each testing result is translated to a 28-day flexural strength
(28-day equivalent laboratory maturity) using a developed mix-specific
flexural strength (third-point loading) versus maturity curve and
equation, and in accordance with the guidelines set forth in the
section titled Using
Maturity Curves and Inter-Strength Relationships to Estimate the
Equivalent 28-day Flexural Strength. (Note: The developed
maturity curve and corresponding equation are included in the
Series A attachments to the PRS [see appendix A in this volume].) No maturity translations
need to be applied if beam specimens are tested directly at a 28-day
equivalent laboratory maturity.
- Compression Testing of Cylinders or Cores. If the concrete
strength of the as-constructed pavement is to be estimated using
cylinder or core specimens tested in compression strength, then the
following procedure applies.
- Each core specimen is tested (at an agency-defined equivalent
laboratory maturity) for compressive strength in accordance with
AASHTO T-24, Obtaining and Testing Drilled Cores and Sawed Beams of
Concrete.(19) Each cylinder specimen is tested (at an
agency-defined equivalent laboratory maturity) for compressive
strength in accordance with AASHTO T-22, Compressive Strength of
Cylindrical Concrete Specimens.(19)
- Each testing result is translated into a 28-day compressive
strength (28-day equivalent laboratory maturity) using a developed
mix-specific compressive strength versus maturity curve and equation,
and in accordance with the guidelines set forth in the section titled
Using
Maturity Curves and Inter-Strength Relationships to Estimate the
Equivalent 28-day Flexural Strength. (Note: The developed
maturity curve and corresponding equation are included in the
Series A attachments to the PRS [see appendix A in this volume].) No maturity translations
need to be applied if cylinder or core specimens are tested directly
at a 28-day equivalent laboratory maturity.
- Each estimated core or cylinder compressive strength (at a 28-day
equivalent laboratory maturity) is translated into a representative
28-day flexural strength using a developed mix-specific compressive
strength to flexural strength inter-strength relationship (curve and
corresponding equation). (Note: The developed inter-strength
relationship is included as a Series B attachment to the PRS
[see appendix A in this volume].)
- Split-Tensile Testing of Cylinders or Cores. If the concrete
strength of the as-constructed pavement is to be estimated using
cylinder or core specimens tested in split-tensile strength, then the
following procedures apply.
- Each core specimen is tested (at an agency-defined equivalent
laboratory maturity) for split-tensile strength in accordance with
AASHTO T-24, Obtaining and Testing Drilled Cores and Sawed Beams of
Concrete.(19) Each cylinder specimen is tested (at an
agency-defined equivalent laboratory maturity) for split-tensile
strength in accordance with AASHTO T-198, Splitting Tensile
Strength of Cylindrical Concrete Specimens.(19)
- Each testing result is translated to a 28-day split-tensile
strength (28-day equivalent laboratory maturity) using a developed
mix-specific split-tensile strength versus maturity curve and
equation, and in accordance with the guidelines set forth in the
section titled Using
Maturity Curves and Inter-Strength Relationships to Estimate the
Equivalent 28-day Flexural Strength.(Note: The developed
maturity curve and corresponding equation are included in the
Series A attachments to the PRS [see appendix
A in this volume].) No maturity translations need to be applied if
cylinder or core specimens are tested directly at a 28-day equivalent
laboratory maturity.
- Each estimated core or cylinder split-tensile strength result (at
a 28-day equivalent laboratory maturity) is translated into a
representative 28-day flexural strength using a developed mix-specific
split-tensile strength to flexural strength inter-strength
relationship (curve and corresponding equation). (Note: The developed
inter-strength relationship is included as a Series B
attachment to the PRS [see appendix
A in this volume].)
Measuring
Maturity in the As-Constructed Pavement
If the agency selects core specimens as the sampling type, the maturity
of the as-constructed pavement is monitored for each sublot. Temperatures
are measured at one central location per sublot using a thermocouple
placed at mid-depth of the pavement slab (the thermocouple is embedded
into the pavement using an agency-approved method). The thermocouple is
connected to an agency-approved maturity meter. The maturity meter should
begin recording pavement temperatures at the time when the thermocouple
becomes completely covered with concrete. Temperatures are measured for a
given sublot until all of the cores representing the sublot are extracted
from the as-constructed pavement.
Using
Maturity Curves and Inter-Strength Relationships to Estimate the
Equivalent 28-day Flexural Strength
As stated earlier, the strength measured for each sampled concrete
strength specimen must be translated into an equivalent 28-day (28 days of
equivalent laboratory maturity) flexural strength. The procedures for
estimating this 28-day flexural strength differ depending on the
agency-chosen sample type, test type, and timing of testing. The general
procedure used to determine an appropriate equivalent 28-day flexural
strength value (for a given sample specimen) involves using the following
procedures. All testing is conducted using the agency-chosen testing
method.
- Conduct the as-constructed strength testing at an agency-chosen
maturity (MATA) to obtain a measured strength value
(STRMEASURED- MAT(A)).
- Determine the expected strength value at the agency-chosen
MATA using the appropriate maturity curve. Note that the
appropriate maturity curve is that developed for the agency-chosen
testing method (i.e., if the agency chooses to conduct compressive
testing of cylinder sample specimens, then the compressive strength
versus maturity curve is used).
- Compute the difference (DIFFMAT(A)) between the measured
strength testing value and the expected strength value (both determined
at the agency-chosen MATA) using equation 14.
DIFFMAT(A) = [STRMEASURED- MAT(A)
– STREXPECTED- MAT(A)](14)
where
DIFFMAT(A) = Computed difference between the
measured strength value and the expected strength value. Strength is
measured in units of MPa.
STRMEASURED- MAT(A) =
Measured strength value at the agency-selected equivalent laboratory
maturity. Strength is measured in units of
MPa.
STREXPECTED- MAT(A) = Expected strength
value (from the appropriate maturity curve) at the agency-selected
equivalent laboratory maturity. Strength is measured in units of
MPa.
- Determine the expected strength at an equivalent laboratory maturity
of 28 days (MAT28 days) from the appropriate maturity
curve.
- Compute the estimated representative strength at an equivalent
laboratory maturity of 28 days (MAT28 days) by adding the
computed strength difference (DIFFMAT(A)) to the expected
28-day expected strength. This relationship is shown in equation
15.
STRESTIMATED-MAT(28 days) = [STREXPECTED-
MAT(28 days) + DIFFMAT(A)]
(15)
where
STRESTIMATED- MAT(28 days) = Estimated equivalent
28-day strength value (strength type is the same as the agency-chosen
testing type) at an equivalent laboratory maturity of 28 days.
Strength is measured in units of MPa.
STREXPECTED- MAT(28
days) = Expected strength value (from the appropriate
maturity curve) at an equivalent laboratory maturity of 28 days.
Strength is measured in units of
MPa.
DIFFMAT(A) = Computed difference between
the measured strength value and the expected strength value. Strength
is measured in units of MPa.
Figure 14 shows an example of translating from a measured strength
value to an equivalent 28-day maturity value of the same strength type
(i.e., the procedure outlined in these first five steps).
- Translate the estimated 28-day strength value for the agency-chosen
testing type (STRESTIMATED(28 days)) into an equivalent
28-day flexural strength (third-point loading) value using an
appropriately developed inter-strength relationship equation.
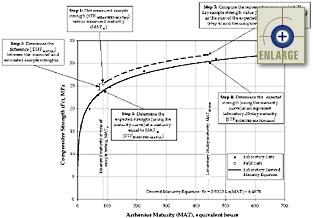 |
|
Figure 14. Example of using a developed
maturity curve to translate from a measured strength value to a
representative 28-day expected strength
value. |
Finally, the mean of all of the estimated equivalent 28-day flexural
strength values (representing each sample specimen from one sample
location) is computed and used to represent that sample location. Some of
the steps of the procedure may not be required, depending on the
agency-chosen sampling and testing procedures.
Slab
Thickness
Two of the distress indicator models (transverse
joint faulting and transverse fatigue cracking) included in the current
PRS approach require slab thickness as an input. The thickness of the
as-constructed pavement is determined by measurements taken on cores
extracted from each sublot making up an as-constructed pavement lot. Core
specimens are extracted from the hardened pavement slab between 48 and 72
hours after placement, in accordance with AASHTO T-24, Obtaining and
Testing Drilled Cores and Sawed Beams of Concrete.(19) All
cores used for the acceptance of slab thickness must have a minimum
diameter of 102 mm. The representative thickness of each core is
determined in accordance with AASHTO T-148, Measuring Length of Drilled
Concrete Cores.(19)
Slab thickness is measured on
all cores extracted for the evaluation of concrete strength; these
measured values are used in lieu of extracting additional slab thickness
cores. When required, randomly selected slab thickness core locations
(independent of any cores taken for the evaluation of concrete strength)
are determined in accordance with the section titled Selecting
a Random Core Location. The number of slab thickness core
specimens per sublot is defined by the agency in accordance with the
guidelines set forth in the section titled Recommended
Number of AQC Samples Per Sublot.
Entrained Air
Content
The measured entrained air content of the pavement slab
is included as an optional input in the transverse joint spalling model
included in the current PRS approach. Although it is officially considered
optional, it is recommended that the agency choose to measure entrained
air content if transverse joint spalling is to be included in the
definition of pavement performance. If entrained air content is selected
for measurement in the field, the following sampling and testing
procedures apply.
The entrained air content of the as-constructed
pavement is determined using one of the following agency-approved sampling
and testing methods:
- Pressure Meter Tests of Plastic Concrete. Plastic concrete is
taken from in front of or behind the paver at predetermined random
longitudinal sampling locations. Random longitudinal sampling locations
are identified in accordance with the guidelines set forth in the
section titled Selecting
a Random Longitudinal Sampling Location. If beams or cylinder
specimens are required for the estimation of concrete strength,
entrained air content pressure meter tests may be conducted at the same
longitudinal locations used for the strength investigation. If
behind-the-paver samples are chosen, material is removed from the slab
using an agency-approved method.
If the agency believes there is
a significant difference between the air content of the material in
front of and behind the paver, it is recommended that the samples be
taken behind the paver. Instead of taking all samples behind the
paver, the agency may develop a relationship between entrained air
content in front of and behind the paver. Samples may then be
taken in front of the paver, and adjusted using the developed
relationship. Samples taken behind the paver should ideally be
taken within a vibrator path.
The plastic concrete removed from
in front of or behind the paver is tested with an agency-approved air
pressure meter in accordance with AASHTO T152, Air Content of Freshly
Mixed Concrete by the Pressure Method.(19) The number of
pressure meter tests per sampling location (replicate specimens) and the
number of sampling locations per sublot are defined by the agency in
accordance with the guidelines set forth in the section titled Recommended
Number of AQC Samples Per Sublot.
Representative
entrained air content values (expressed as a percentage) for each
sample per sublot are computed as the average of the entrained
air content results determined for the replicate specimens at each
random sampling location.
- Linear Traverse Tests of Hardened Concrete Cores. Core
specimens are extracted from the hardened concrete slab at predetermined
random sampling locations. Random sampling core locations are determined
in accordance with the guidelines set forth in the section titled Selecting
a Random Core Location. Core specimens are extracted from the
hardened pavement slab, between 48 and 72 hours after placement, in
accordance with AASHTO T-24, Obtaining and Testing Drilled Cores and
Sawed Beams of Concrete.(19) All cores used for the
acceptance of entrained air content must have a minimum diameter of 152
mm. The number of core specimens per sublot are defined by the agency in
accordance with the guidelines set forth in the section titled Recommended
Number of AQC Samples Per Sublot.
Linear traverse testing
is performed on each extracted hardened concrete core specimen in
accordance with ASTM C-457, Standard Test Method for Microscopical
Determination of Parameters of the Air-Void System in Hardened
Concrete.(20) Testing may occur at any time after the
extraction of the core specimen. The measured entrained air content
(expressed as a percentage) for each extracted core is used as the
representative entrained air content value for that sampling
location.
Initial Smoothness
The two smoothness-related distress
indicator models (PSR and IRI) included in the current PRS approach
require initial smoothness as an input. The PSR distress indicator model
requires an initial PSR, whereas the IRI model requires an initial IRI.
The selection of an initial smoothness sampling and testing plan requires
that the agency answer the following three questions:
- What type of initial smoothness measuring device is to be
used? The agency may measure initial smoothness with a California or
similar profilograph (used to compute a profile index [PI]) or an
inertial profiler (used to compute IRI).
- What type of initial smoothness indicator is to be computed?
If the agency chooses to measure initial smoothness using a California
profilograph, the agency may reduce the profile traces using a 0.0-mm or
a 5.1-mm blanking band. The 0.0-mm blanking band is strongly recommended
over the 5.1-mm blanking band. Pavements accepted using a 5.1-mm
blanking band may still be quite rough to the driver, and this is not
adequate. These reductions result in the computing of corresponding
profile indices (PI0.0-mm and PI5.1-mm,
respectively). If the agency chooses to measure initial smoothness using
an inertial profiler, the initial smoothness indicator is expressed in
terms of IRI.
- Is smoothness over time to be expressed in terms of PSR or
IRI? Finally, the agency has the option of predicting smoothness
over time in terms of PSR or IRI. A correlation between PI and PSR or
IRI is required.
Figure 15 shows the relationships
between these three agency decisions. The following sections provide
details regarding the sampling and testing of initial smoothness.
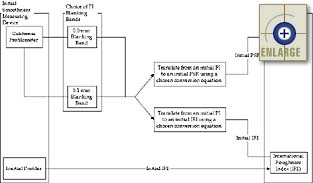 |
|
Figure 15. Flow chart showing the
available methods for handling smoothness under the PRS
approach. | Sampling of Initial
Smoothness
The initial smoothness of the pavement is quantified
in terms of a PI (using a California profilograph) or IRI (using an
agency-approved inertial profiler). If a California profilograph is used,
the measurements are made in accordance with the following procedures:
- The resulting profilogram is to be recorded on a scale of 254 mm or
full-scale, vertically.
- Motive power may be manual or by propulsion unit attached to the
assembly.
- The profilograph is moved longitudinally along the pavement at a
speed no greater than 4.8 km/h to minimize bounce.
- The results of the profilograph test will be evaluated as outlined
in the California Department of Transportation (Caltrans) specification
CA-526.
- All profile indices are to be determined using a 0.0- or 5.1-mm
blanking band.
If a profiling device is used to measure initial IRI, measurement is
made in accordance with provided agency-approved
procedures.
Regardless of the chosen sampling method, a minimum of
two pavement profiles (one in each wheelpath) must be measured for each
lane within each defined sublot. The total number of required pavement
profiles per sublot is defined by the agency in accordance with the
guidelines set forth in the section titled Recommended
Number of AQC Samples Per Sublot. The location of a
wheelpath is 0.92 m from a longitudinal joint or longitudinal
pavement edge and parallel to the centerline of the mainline paving. For
widened traffic lanes, the outer wheelpath is 0.92 m from the
pavement-edge paint stripe, rather than the outer pavement edge. Each
profile should terminate 4.5 m from each bridge approach pavement or
existing pavement that is joined by the new pavement. The PI or IRI
determined for each profile is converted to a standard unit of
mm/km.
During the initial paving operations, or after a long
shutdown period, the pavement surface must be tested with the appropriate
profile measuring device. Membrane curing damaged during the testing
operation must be repaired by the contractor and at the contractor's
expense. If the initial pavement smoothness, paving methods, and paving
equipment are acceptable, paving operations may proceed. After initial
testing, profiles of each day's paving will be run prior to continuing
paving operations.
The agency will apply the following appropriate
limits based on the chosen initial smoothness indicator (PI or IRI):
If an average PI / IRI of _____ mm/km [limit to be inserted by the
agency] is exceeded in any daily paving operation, the paving operation
will be suspended and not resume until corrective action is
taken.
Within each sublot, all areas represented by high points having
deviations in excess of _____ mm (limit to be inserted by the agency—10 mm
is recommended) in 7.6 m or less must be corrected at the contractor's
expense. Corrections must be made using an approved profiling device or by
removing and replacing the pavement, as directed by the engineer. Bush
hammers or other impact devices must not be used. Where corrections are
made, the surface texture is re-established to provide a uniform texture
equal to the surrounding uncorrected pavement by the contractor and at the
contractor's expense.
Choosing an Appropriate Blanking Band for
Computing Profile Index
When measuring initial smoothness using
a California profilograph, the resulting profilograms may be reduced using
a 0.0- or 5.1-mm blanking band. Currently, most SHA's measure initial
smoothness in terms of PI5.1-mm; however, more agencies are
starting to move toward using PI0.0-mm. As mentioned
previously, it is strongly recommended to use the PI0.0-mm as
it provides better control over initial smoothness.
Converting
From a Profile Index to an Initial PSR or IRI
Under the PRS
approach, if an agency decides to measure initial smoothness in terms of
PI0.0-mm, the agency must develop their own conversion equation
from PI0.0-mm to initial PSR or IRI. Unfortunately, there is
little published information regarding such conversion equations. If the
agency does not wish to develop a relationship based on
PI0.0-mm, initial smoothness may be measured in terms of
PI5.1-mm and converted to an initial PSR or IRI using an
available conversion equation. Many such relationships have been developed
under past research. Some of the currently available PI5.1-mm
to initial PSR and PI5.1-mm to initial IRI relationships are
summarized in tables 6 and 7. The agency-chosen relationship is an input
in the PaveSpec 2.0 computer software.
Table 6.
Published relationships between measured PI (using a 5.1-mm blanking band)
and initial PSR.(21)
Equation |
Source |
PSR = 5.0 – 0.0714(PI5.1-mm) |
Darter et al.(2) |
PSI = –0.04762(PI5.1-mm) + 4.443 |
Walker and Lin(22) |
PSI = 4.06 – 0.0256(PI5.1-mm) |
Uddin, Hudson, and
Elkins(23) |
Note: Present serviceability index (PSI) is
used interchangeably with PSR. Also, the PI required by these equations is
expressed in units of in/mi.
Table 7.
Published relationships between measured PI (using a 5.1-mm blanking band)
and initial IRI.
Equation |
Source |
IRI = 52.9 + 6.0(PI5.1-mm) |
Kombe and Kaleva(24) |
IRI = 73.7 + 2.83(PI5.1-mm) |
Kombe and Kaleva(24) |
PIa.p. = –22.3 + 0.3(IRI) |
Goulias, Dossey, and Hudson(25) |
IRI = 36.4 + 3.11(PI5.1-mm)(for PI=5-7
in/mi) |
Kulakowski and
Wambold(26) |
Note: The PI required by these equations is
expressed in units of in/mi. 1.0 in/mi = 15.78 mm/km
Measuring Initial Smoothness in Terms of IRI
If the
agency chooses to measure initial smoothness in terms of IRI (directly),
the only available option is to predict smoothness over time in terms of
IRI (see figure
15). Although there are currently no reliable methods for measuring
initial IRI on newly placed concrete, research continues in this area. In
anticipation of the development of such an initial IRI measurement method,
this option was included in the revised PRS prototype.
Percent
Consolidation Around Dowels
The measured percent consolidation
around dowels is included as an optional input in the transverse joint
faulting model included in the current PRS approach. If percent
consolidation around dowels is selected for measurement in the field, the
following sampling and testing procedures apply.
The representative
percent consolidation around one randomly selected dowel bar in a sublot
is determined based on a comparison of the density of two selected cores
extracted from the hardened concrete slab. Core specimens are extracted
from the hardened pavement slab between 48 and 72 hours after placement,
in accordance with AASHTO T-24, Obtaining and Testing Drilled Cores and
Sawed Beams of Concrete.(19) All cores used for the
acceptance of percent consolidation around dowels must have a minimum
diameter of 102 mm.
The first of the two required cores is taken
through a predetermined randomly selected dowel bar in a randomly selected
transverse joint (random sampling core locations are determined in
accordance with the guidelines set forth in the section titled Selecting
a Random Dowel Location). The outside edge of the core through the
randomly selected dowel bar must not be within 60 mm of a defined
wheelpath or pavement edge, 100 mm of a vibrator path, or 50 mm of a
transverse joint. The dowel bar piece is separated from the concrete core
material by an agency-approved method. The density of this concrete
material is measured in a saturated surface dried condition in accordance
with ASTM C-642, Standard Test Method for Specific Gravity, Absorption,
and Voids in Hardened Concrete(20), and labeled as
DENTHROUGH-DOWEL(n).
The second of the two required
cores is taken at a location along a line passing through the first core
(through the dowel bar) and parallel to the centerline of the pavement
unit. The specific longitudinal location of this second core is assumed to
be at midslab of the leave slab (the slab away from the joint in the
direction of traffic) adjacent to the randomly selected transverse joint.
The density of this concrete material is measured in a saturated surface
dried condition in accordance with ASTM C-642, Standard Test Method for
Specific Gravity, Absorption, and Voids in Hardened
Concrete(20), and labeled as the
DENMID-SLAB(n).
The number of samples per sublot (i.e.,
pairs of cores) is defined by the agency in accordance with the guidelines
set forth in the section titled Recommended
Number of AQC Samples Per Sublot. The maximum of all of the
midslab core densities measured within the given lot
(MAX-DENMID-SLAB) is determined and assumed to represent the
density of a core with 100 percent consolidation. The representative
percent consolidation for each sampling location (set of cores) is,
therefore, determined using equation 16.
%Consolidation=(DENTHROUGH-DOWEL(n)
/MAX-DENMID-SLAB)*100 (16)
Retesting Procedures
Additional sampling and testing for any of the AQC's for acceptance
testing may be requested at any time by the contractor or by the agency.
Retesting is, however, required if any AQC test results are found
to be of lesser quality than agency-defined rejectable quality limits
(RQL's). These limits define the minimum quality allowed to stay in place
(and subjected to a pay adjustment) on the as-constructed pavement. For
concrete strength, slab thickness, air content, and percent consolidation
around dowels, retesting is required if the measured sample value is
less than the defined RQL; however, for initial smoothness,
retesting is required if the measured sample value is greater than
the defined RQL.
At the same time, the agency defines maximum
quality limits (MQL's) to be applied to each AQC specimen sample value.
The MQL's define the limit on the additional quality (beyond the target
values) for which the agency is willing to pay an incentive. Therefore, if
a specimen sample value is measured to be of greater quality than the
defined MQL, the representative specimen sample value (used in the
acceptance procedures) is set equal to the defined MQL (i.e., the
contractor will not receive credit for quality provided in excess of the
MQL). For concrete strength, slab thickness, air content, and percent
consolidation around dowels, the MQL is an upper limit on quality;
however, for initial smoothness, the MQL is a lower limit on
quality.
The purpose of retesting is to determine if the AQC
quality provided by the contractor is truly less than the quality defined
by the RQL. If retesting procedures determine conclusively that an
identified area of pavement is deficient in quality (having lesser quality
than the respective agency-defined RQL), the result will be the removal
and replacement of the identified area. AQC sampling and testing values
from the replaced material is then used in replacement of the original
sampling and testing results for that sampling location. However, the AQC
samples taken from the replaced material are subjected to MQL's equal to
the respective AQC target values (i.e., the contractor may not get credit
for AQC quality better than the target values when material has been
removed and replaced).
If retesting procedures determine
conclusively that an identified area of pavement is not deficient in
quality (having greater quality than the respective agency-defined RQL),
the additional AQC samples taken for retesting are added to the original
AQC sample value set. The average of all the AQC sampling and testing
results (original and retesting) representing a sampling location is then
used as the representative AQC value for that sampling location. If the
contractor and agency agree that a testing error occurred when determining
an AQC test value, this test value is excluded from the acceptance
process.
Selection of Appropriate RQL's and MQL's
The
agency should choose RQL and MQL values carefully, so they truly define
the range of AQC quality that the agency desires. The selected RQL's
should identify the absolute minimum quality that the agency will accept
as part of the as-constructed pavement. Any lesser quality pavement will
be removed and replaced. The selected MQL's should identify the absolute
maximum quality for which the agency is willing to pay an incentive. These
quality limits provide the agency with a method of defining practical
limits that keep the focus of the contractor on the as-designed target
quality values. In turn, the contractor knows exactly how much additional
quality he can provide (in excess of the AQC target values) and still
expect to get paid an incentive. Again, it is important to stress that
under the PRS approach, the AQC target values represent the true
agency-desired quality.
All AQC test values that are measured to be
between the agency-defined RQL and MQL will be kept in place and used for
acceptance. Pay adjustments are determined and based on this measured AQC
quality.
Specific Retesting Responsibilities
The
specific retesting procedures are identified by the agency and provided as
part of the specification. The agency will conduct all of the sampling and
testing for any retesting activities. The conditions for determining
whether the agency or contractor is responsible for the cost of the
retesting will be determined in accordance with the specific retesting
procedures provided in the specification. The pavement may only be
retested once in accordance with the retesting methods provided in the
specification. The sublot retesting sampling locations are determined in
accordance with the guidelines set forth in the section titled Selection
of Random Sampling Locations.
Recommended
Number of AQC Samples Per Sublot
The number of AQC samples per sublot has a large effect on the risks to
the agency and contractor. The recommended number of samples per sublot
(for each AQC) is specific to the chosen sampling and testing method.
Figure 16 shows the effect of the number of samples per sublot on the
as-designed present worth LCC standard deviation for a typical example (3
sublots per lot, 500 lots per simulation). Each point on the chart
represents the standard deviation of 500 simulated lot LCC's. This
computed standard deviation is an indicator of the risks or uncertainty
involved in estimating the LCC from small sample sizes.
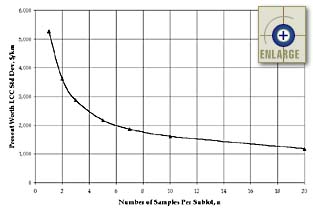 |
|
Figure 16. Example showing the typical
effects of number of samples per sublot on the LCC standard
deviation (3 sublots per lot, 500 lots per simulated
point) |
The points making up the chart in figure 16 were simulated by setting
four different AQC's (concrete strength, slab thickness, entrained air
content, and initial smoothness; percent consolidation around dowels was
not included in this example) equal to their target means and standard
deviations. At each simulation point, all of the included AQC's used the
sample size reflected in the chart (i.e., for the simulated point where n
= 10, 10 samples per sublot were taken for each of the four included
AQC's).
Figure 16 shows that there is great benefit of using more
than one sample per sublot. It also shows that the LCC standard deviation
tends to stabilize for sample sizes greater than or equal to five.
Therefore, it is recommended that sample sizes of two to five samples per
sublot be used for acceptance in the field. It is, however, recognized
that it may not be practical to take three to five samples per sublot for
all AQC sampling types (e.g., linear traverse testing for entrained air
content). Hence, it is recommended that the agency select AQC sample size
by balancing the risk of errors in quality determination with the
practicality and cost of sampling and testing. It is important to note
that regardless of the number of samples per sublot chosen for each AQC,
the selected number of AQC samples per sublot will be the same for both
as-constructed and as-designed simulations. Therefore, the same effects of
simulation error or bias on the simulated LCC's will be present in both
the as-constructed and as-designed representative LCC means. Table 8 shows
recommended minimum number of samples per lot for different AQC sampling
and testing types.
Table
8. Recommended minimum number of samples per sublot for different sampling
and testing methods.
AQC |
Sample Type |
Testing Type |
Recommended Minimum Number
of Sampling Locations per Sublot, n |
Recommended Minimum Number
of Replicate Samples per Sampling Location |
Concrete Strength |
Beams |
28-day modulus of rupture |
2–5 |
2 |
Early age modulus of rupture |
Cylinders |
28-day compressive |
2–5 |
2 |
Early age compressive |
8-day split-tensile |
Early age split-tensile |
Cores |
28-day compressive |
2–5 |
N/A |
Early age compressive |
28-day split-tensile |
Early age split-tensile |
Slab Thickness |
Cores |
N/A |
2–5 |
N/A |
Entrained Air Content |
Fresh Concrete |
Air pressure meter |
3–5 |
2 |
Cores |
Linear traverse |
1–3 |
N/A |
Initial Smoothness |
Profile Index |
California profilograph |
2 times the number of lanes (inner and outer
wheelpaths of each lane) |
None |
IRI |
Inertial profiler |
2 times the number of lanes (inner and outer
wheelpaths of each lane) |
None |
Percent Consolidation Around Dowels |
Pairs of Cores |
Relative density comparison |
1–3 |
None |
Note: IRI = international
roughness index
Selection of Random
Sampling Locations
Selecting a
Random Longitudinal Sampling Location
Random longitudinal sampling locations need to be identified whenever
concrete strength or entrained air content is determined using samples of
plastic concrete. Plastic concrete will be taken from in front of the
paver (or behind the paver for air content, if so desired) at every
randomly determined longitudinal sampling location. These estimated
sampling locations are determined for each sublot in a given lot prior to
the start of the paving of that lot (typically, these longitudinal
sampling locations are determined on a day-to-day basis, before the start
of that day's paving). Each specific required longitudinal sampling
location (within a given sublot) may be determined using the following
procedures:
- Determine one random number (between 0 and 1) using an
agency-approved random number generation method.
- Identify the target sublot length (PAVINGSUBLOT)
(expressed in meters).
- Multiply the random number by PAVINGSUBLOT to determine
the longitudinal offset from the sublot's starting
station.
As an example, let us assume that we have a project with a target
sublot length of 200 m (PAVINGSUBLOT = 200 m). A random number
is generated to be 0.422 using an agency-approved random generation
method. Therefore, the longitudinal offset from the sublot's starting
station is computed as 200 m * 0.422 = 84.4 m. This example is illustrated
in figure 17.
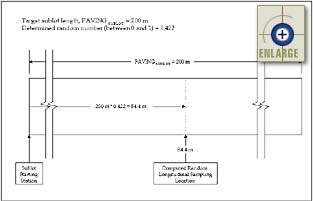 |
|
Figure 17. Example of locating a randomly
selected longitudinal sampling
location. |
Selecting a Random Core
Location
Random core sampling locations need to be identified whenever concrete
strength, slab thickness, or entrained air content is estimated based on
core samples taken from the hardened concrete slab. These estimated core
sample locations are determined within each sublot in a given lot prior to
the start of the paving of that lot. Again, these random core locations
are typically determined on a day-to-day basis, before the start of that
day's paving. Each random core location requires the determination of a
longitudinal and horizontal offset within a sublot. Each specific required
core location (within a given sublot) may be determined using the
following procedures:
- Determine two random numbers (between 0 and 1) using an
agency-approved random number generation method.
- Identify the target sublot length (PAVINGSUBLOT)
(expressed in meters).
- Identify the lot width (the width of the construction pass)
(expressed in meters).
- Multiply the first random number by PAVINGSUBLOT to
determine the core's longitudinal offset from the sublot's starting
station.
- Multiply the second random number by the lot width to determine the
core's horizontal offset from the construction pass outside edge (the
edge closest to the outer shoulder).
This process is demonstrated by the following example:
- Determined random numbers: 0.345 and 0.645.
- Agency-chosen target sublot length (PAVINGSUBLOT): 200
m.
- Lot width: 7.32 m.
The longitudinal offset is calculated to be 200 m * 0.345 = 69 m, and
the horizontal offset from the outer edge is calculated to be 7.32 m *
0.645 = 4.7 m. The agency may choose to apply restrictions to the randomly
generated core locations to avoid sampling near joints or directly in the
wheelpaths. This example is illustrated in figure 18.
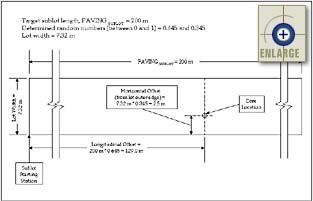 |
|
Figure 18. Example of locating a randomly
selected core location. |
Selecting a Random Dowel
Location
The selection of a random dowel location for the testing of percent
consolidation around dowels first involves the selection of a random
transverse joint, followed by the selection of a random dowel bar within
the selected transverse joint. Each required core location (within a given
sublot) may be determined using the following procedure:
- Determine two random numbers (between 0 and 1) using an
agency-approved random number generation method.
- Identify the target sublot length (PAVINGSUBLOT)
(expressed in meters).
- Define the average transverse joint spacing (expressed in
meters).
- Determine the number of dowel bars to be placed within one
transverse joint.
- Determine the number of actual transverse joints expected to fall
within the target sublot length, computed by dividing
PAVINGSUBLOTby the chosen average transverse joint
spacing.
- Multiply the first random number by the number of actual transverse
joints observed to fall within the given sublot. Round this number to
the nearest integer.Number the transverse joints (consecutively) within
the sublot, and use the determined integer to locate the transverse
joint to be investigated.
- Multiply the second random number by the number of dowel bars placed
within one transverse joint. Round this number to the nearest integer.
Number the dowel bars (consecutively) within the transverse joint, and
use the determined integer to locate the dowel bar to be
investigated.
This process is demonstrated by the following example:
- Determined random numbers: 0.246 and 0.302.
- Agency-chosen target sublot length (PAVINGSUBLOT): 200 m.
- Average transverse joint spacing: 4.57 m.
- Number of dowel bars in one transverse joint: 23.
First, the number of actual transverse joints in the sublot with a
length equal to PAVINGSUBLOT is computed to be 43.8 joints by
dividing PAVINGSUBLOT by the chosen average transverse joint
spacing (i.e., 200 m/4.57 m = 43.8 joints). This computed value is then
rounded down to 43 and used as the number of joints appearing in the
sublot. After the 43 joints are numbered consecutively in the sublot, the
computed number of joints (43 joints) is then multiplied by the first
random number (0.246) to determine the selected transverse joint for
investigation. For this example, this specific joint is determined as 43
joints * 0.246 = 10.6 joints (rounded to 11). Therefore, the eleventh
joint in the sublot is chosen to conduct the percent consolidation
sampling.
Next, the specific dowel bar to be investigated must be
determined. After the 23 dowel bars are numbered for the joint (starting
at the outer edge), the second random number (0.302) is multiplied by the
number of dowel bars in one transverse joint (23) to determine the
specific dowel bar for investigation. This dowel bar is determined to be
0.302 * 23 = 6.95, which is then rounded to 7. Therefore, for this
example, dowel bar #7 of transverse joint #11 is investigated for percent
consolidation. This example is illustrated in figure 19.
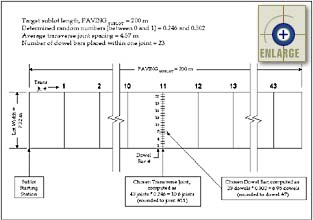 |
|
Figure 19. Example of locating a randomly
selected dowel bar for the investigation of percent consolidation
around dowels. |
Selecting a
Maintenance and Rehabilitation Plan |
 |
 |
The agency must identify an M & R plan for use in the PRS approach.
The agency is encouraged to define an M & R plan that closely
resembles that actually used in the field. An M & R plan consists of
identifying the type and frequency of routine maintenance, localized
rehabilitation, and global rehabilitation activities. More information on
each of these categories is included below.
Maintenance Activities
The current PRS approach limits routine maintenance activities to the
following three:
- Transverse joint sealing.
- Longitudinal joint sealing.
- Transverse crack sealing.
The agency must decide which of these three activities (if any) are to
be included in the yearly M & R cost calculations. For each chosen
maintenance activity, the agency must define the frequency of maintenance
application (in terms of years). For example, the agency may choose to
seal transverse joints every 3 years, whereas transverse crack sealing may
be addressed every year. In addition to determining the frequency of
maintenance application, the agency must also identify the amount of
maintenance to be applied during each visit to the field. The agency
answers this question by identifying the percentage of joints or cracks to
seal at each scheduled visit to the field.
Local Rehabilitation
Activities
Localized rehabilitation activities are defined as those that may be
used to correct localized pavement distresses. Localized distresses
are defined as those that may affect an individual joint (transverse joint
spalling and transverse joint faulting) or slab (transverse slab
cracking). The current PRS approach provides the agency with the following
choices for localized rehabilitation activities as they relate to the
respective distresses:
- Transverse joint spalling may be addressed with full- or
partial-depth repairs.
- Transverse slab cracking may be addressed with full or
partial slab replacements.
As with the chosen routine maintenance activities, the agency must
define which local rehabilitation activities to apply and when to apply
them. This is accomplished by the following three steps:
- The agency must select one of the available localized rehabilitation
activities to address every one of the three distress indicators
(transverse joint spalling, transverse joint faulting, and transverse
slab cracking) chosen to define pavement performance.
- The agency must decide at what frequency to apply these localized
rehabilitation activities. Under the current PRS approach, the frequency
of each selected activity is defined in terms of years (i.e., transverse
slab cracking is addressed with full-depth slab replacements that are
applied every 5 years).
- The agency must decide how much of the required localized
rehabilitation to apply at each application year (application years are
defined by the chosen application frequency). For example, instead of
repairing 100 percent of the predicted cracked slabs every 5 years, an
agency may choose to only correct 50 percent of the cracked slabs in any
one localized rehabilitation application year.
The agency is encouraged to define a localized rehabilitation plan that
closely resembles the rehabilitation activities actually used by the
agency in the field.
Global Rehabilitation
Activities
Global rehabilitation activities are those activities that are applied
to the entire lot (all sublots within the lot) at one time in response to
declining global pavement conditions. These activities are
specifically applied to address pavement condition indicators such as
decreasing pavement smoothness (IRI or PSR), increasing amounts of
localized distress, or increasing amounts of applied localized
rehabilitation. Trigger values for these pavement condition indicators are
typically defined to determine the timing of a global rehabilitation. The
current PRS approach limits the global rehabilitation activities to the
following three:
- AC overlays.
- PCC overlays.
- Diamond grinding.
As with the chosen localized maintenance activities, the agency must
define which global rehabilitation activity to apply and when to apply it.
This is accomplished by the following three steps:
- The agency must select one of the three available global
rehabilitation policies to address deteriorating global
conditions.
- The agency must define the method used to determine the timing of
the first scheduled global rehabilitation. The current PRS approach
allows the agency to base the timing of this first global rehabilitation
on either lot threshold trigger values (on distress or localized
rehabilitation values) or the computed PSF. It is recommended that the
first year of lot global rehabilitation be determined using the PSF
concept. More details are provided on these decisions in chapter 4,
within the section titled Calculation
of the Representative LCC for a Given Lot.
- The agency must define an expected life of the chosen global
rehabilitation. Rather than predict pavement performance after the first
applied global rehabilitation, the current PRS approach assumes that
subsequent global rehabilitations (of the same global rehabilitation
type) will be applied at a fixed time interval equal to the chosen
global rehabilitation life.
Again, the agency is encouraged to define a global rehabilitation plan
that closely resembles the rehabilitation activities actually used by the
agency in the field.
Cost-Related
Decisions |
 |
 |
Maintenance and
Rehabilitation Unit Costs
The agency must define unit costs for each of the M & R activities
chosen for inclusion in the M & R plan. These selected unit costs,
combined with knowledge of the predicted yearly distresses, allow for the
calculation of the yearly M & R costs. The unit costs for the possible
M & R activities are typically expressed in the following
formats.
Maintenance Unit Costs
- Transverse joint sealing—Dollars per linear meter of sealing or
dollars per transverse joint.
- Longitudinal joint sealing—Dollars per linear meter of sealing.
- Transverse crack sealing—Dollars per linear meter of sealing or
dollars per transverse crack.
Localized Rehabilitation Unit Costs
- Full-depth joint repairs—Dollars per square meter or dollars per
transverse joint.
- Partial-depth joint repairs—Dollars per square meter or dollars per
transverse joint.
- Full slab replacements—Dollars per square meter or dollars per
slab.
- Partial slab replacements—Dollars per square
meter.
Global Rehabilitation Unit Costs
- AC overlays—Dollars per square meter.
- PCC overlays—Dollars per square meter.
- Diamond grinding—Dollars per square meter.
It is recommended that current agency cost records be reviewed in order
to obtain the most accurate unit cost values possible for each of the
chosen M & R activities.
Inclusion of User
Costs
Under the current PRS approach, the agency has the option to include
user costs in the pay factor determination process. User costs are
expressed in dollars per kilometer per vehicle and are made up of the
following four components:
- Accident.
- Delay from roughness (not from lane closures).
- Discomfort.
- Vehicle operating.
User costs are calculated for each year based on the predicted pavement
smoothness (PSR or IRI). Details of the user cost calculations are
presented in chapter 4, in the section titled Calculation of
the Representative LCC for a Given Lot.
Under the current
approach, the agency may define a certain percentage of these calculated
yearly user costs to be included in the overall lot LCC. If the agency
does not feel that any user costs should influence the pay factor, this
chosen user cost percentage may be set to zero. However, if user costs are
included, it is recommended that the agency include a specific percentage
that results in pay factors with which the agency is comfortable.
Typically, user cost percentages up to 5 percent have resulted in
reasonable pay factors. Larger percentages result in pay adjustments that
are quite high.
Selecting a Discount
Rate
The agency is required to select a discount rate to be used in
determining PW LCC’s. As defined previously, the discount rate is
estimated as the difference between the interest and inflation rates,
representing the real value of money over time. This relationship is shown
below in equation 17.
DISCOUNT = INTEREST – INFLATION
(17)
where
DISCOUNT = Estimated discount rate,
percent.
INTEREST = Estimated interest rate,
percent.
INFLATION = Estimated inflation rate,
percent.
The interest rate, often referred to as the market interest
rate, is associated with the cost of borrowing money and represents the
earning power of money.(10) The inflation rate is typically
defined as the rate of increase in the prices of goods and services
(construction of highways) and represents changes in the purchasing power
of money.(10) In 1997, FHWA recommended that LCC’s should be
calculated using "a reasonable discount rate that reflects historical
trends over long periods of time."(10) Past research in the
U.S. has revealed that the real long-term rate of return on capital (i.e.,
the discount rate) has generally been between 3 and 5
percent.(10,27) It is recommended that the agency select an
appropriate discount rate value from this 3- to 5-percent range.
Selecting an
Appropriate Bid Price for Developing Level 1
Preconstruction Output |
 |
 |
If the agency chooses to compute lot pay factors using Level 1 pay
adjustment procedures, an appropriate bid price is required to develop the
preconstruction output. This appropriate bid price is required since this
preconstruction output must be developed prior to the project being let
(prior to obtaining any contractor bids). It is recommended that the
agency compute this appropriate bid price as the average of the unit bid
prices observed on similar paving projects during the previous year (in
dollars per square meter). The agency may use data from other past years;
however, those costs should be updated to include the effects of
inflation.
Selecting
Simulation Paramaters |
 |
 |
Number of Simulation
Lots
The generation of preconstruction output involves the simulation of lot
LCC’s. The as-designed lot LCC’s for both Level 1 and Level 2, as well as
the points making up the Level 1 individual AQC pay factor curves, are
determined as the average of "n" simulated lots. Although the simulated
LCC mean is generally found to stabilize when n is greater than 200 to
250, it is suggested that the agency use a representative value of n =
500. Additional simulations beyond n = 500 do not change the mean LCC’s
significantly.
Simulations
for Different Numbers of Sublots Per Lot
Although the sampling and testing plan is easily identified for each
as-constructed sublot, it is not as easy to identify the number of sublots
that will make up each as-constructed lot in the field. The number of
actual as-constructed sublots will most likely vary from lot to lot (day
to day) due to changes in weather, plant and paver equipment problems, and
other factors. Because the simulated preconstruction output (Level 1
individual AQC pay factor curves and the Level 2 as-designed target LCC)
is dependent on the number of sublots per lot, this preconstruction output
must then be simulated for the different numbers of projected sublots per
lot. This task is easily accomplished within the PaveSpec 2.0 software by
defining the range of number of sublots per lot for which simulations will
be completed.
After determining the target number of sublots per
lot (NUMSUBS—see the section titled Definition
of a Sublot [in chapter 5]), it is recommended that the agency
generate representative preconstruction output for a range of 1 to NUMSUBS
+ 3. For example, if the target number of sublots per lot was estimated as
NUMSUBS = 4, it would be recommended that the agency generate
preconstruction output for the cases of 1 to 7 sublots. If an agency
chooses to simulate only one particular case for use in acceptance, it is
recommended that the preconstruction output resulting from the simulation
of NUMSUBS per lot be used. |