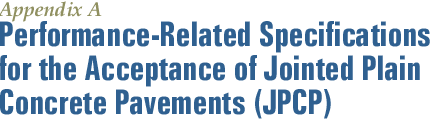
Introduction |
 |
 |
This document provides construction specifications for jointed plain
concrete pavement (JPCP) that includes the measurement of several key
acceptance quality characteristics (AQC's). Each of the AQC's (mean and
standard deviation) is related to performance and, thus, to life-cycle
costs (LCC's) over a chosen analysis period. The incentive/disincentive
pay factors are computed based on expected future performance and
costs.
The format and content of these Performance-Related
Specifications (PRS) are based in part on the following American
Association of State Highway and Transportation Officials (AASHTO) Guide
Specifications for Highway Pavement Construction:
- Guide Specifications for Highway Construction,
1993.(29)
- Quality Assurance Guide Specification, February
1996.(9)
- Implementation Manual for Quality Assurance, February
1996.(28)
Table of
Contents |
 |
 |
DIVISION
100. GENERAL PROVISIONS
SECTION
PRS–101. DEFINITIONS SECTION
PRS–110. QUALITY ASSURANCE PRS–110.01
Samples, Tests, and Referenced Specifications PRS–110.02
Qualified Testing Laboratory PRS–110.03
Technician Certification PRS–110.04
Quality Control PRS–110.05
Acceptance PRS–110.06
Quality Pay Adjustments PRS–110.07
Dispute Resolution
DIVISION
500. RIGID PAVEMENT
SECTION
PRS–501. JOINTED PLAIN PORTLAND CEMENT CONCRETE PAVEMENT PRS–501.01
Description PRS–501.02
Materials PRS–501.03
Construction Requirements PRS–501.04
Methods of AQC Measurement
A.
Lots B.
Sublots C.
Definition of Pavement Performance D.
Included Acceptance Quality Characteristics E.
Selection of AQC Target Values F.
Identification of AQC Limits for Acceptance G.
AQC Sampling and Testing Methods 1.
Concrete Strength a.
Sampling of Concrete Strength i.
Beams ii.
Cylinders iii.
Cores b.
Timing of Concrete Strength Testing c.
Testing-Related Procedures (Conducted Prior to Specimen
Testing) i.
Laboratory Maturity Calibration ii.
Laboratory-Developed Inter-Strength Relationships iii.
Measuring Maturity in the As-Constructed Pavement d.
Specific Concrete Strength Testing Procedures i.
Flexural Testing of Beams ii.
Compression Testing of Cylinders or Cores iii.
Split-Tensile Testing of Cylinders or Cores e.
Concrete Strength Acceptance 2.
Slab Thickness a.
Sampling and Testing of Slab Thickness b.
Slab Thickness Acceptance 3.
Entrained Air Content a.
Sampling and Testing of Entrained Air Content i.
Pressure Meter Tests of Plastic Concrete ii.
Linear Traverse Tests of Hardened Concrete Cores b.
Entrained Air Content Acceptance 4.
Initial Smoothness a.
Sampling and Testing of Initial Smoothness b.
Initial Smoothness Acceptance 5.
Percent Consolidation Around Dowels a.
Sampling and Testing of Percent Consolidation Around
Dowels b.
Acceptance of Percent Consolidation Around
Dowels
PRS–501.05
Methods of AQC Retesting
A.
Concrete Strength B.
Slab Thickness C.
Entrained Air Content D.
Initial Smoothness E.
Percent Consolidation Around Dowels
PRS–501.06
Basis of Acceptance
A.
Life-Cycle Costs B.
As-Designed Target Pavement C.
As-Constructed Pavement Lot
PRS–501.07
Basis of Payment
A.
Level 1 Pay Adjustment B.
Level 2 Pay Adjustment
ATTACHMENT
SERIES A —LABORATORY MATURITY CALIBRATION CURVES AND RESPECTIVE
EQUATIONS ATTACHMENT
SERIES B —LABORATORY-DEVELOPED INTER-STRENGTH CURVES AND RESPECTIVE
EQUATIONS ATTACHMENT
SERIES C —PROJECT-SPECIFIC CONSTANT VALUES ATTACHMENT
SERIES D —LEVEL 1 INDIVIDUAL AQC PAY FACTOR CHARTS AND
EQUATIONS
DIVISION
100. GENERAL PROVISIONS
SECTION PRS–101. DEFINITIONS |
 |
 |
The following definitions are applicable to this Specification:
Acceptance Quality Characteristics (AQC's): Inherent
measurable pavement characteristics that significantly affect pavement
performance, are under the ULect control of the contractor, and are
measurable at or near the time of construction. AQC's considered under
the current PRS include concrete strength, slab thickness, entrained air
content, initial smoothness, and percent consolidation around dowel
bars.
Analysis Period: Period of time over which future M
& R costs are to be considered in an LCC analysis. The analysis
period is typically defined as twice the chosen initial pavement design
life.
AQC Target Values: Agency-chosen AQC means and
standard deviations that define the agency's desired quality (the AQC
quality for which the agency is willing to pay 100 percent of the bid
price).
As-Constructed Lot Life-Cycle Cost
(LCCCON):The estimated post-construction LCC used to
represent the as-constructed pavement lot quality. This value is based
(in part) on the measured as-constructed AQC values (means and standard
deviations).
As-Constructed Pavement: The actual concrete
pavement constructed by the contractor. The as-constructed quality level
of each pavement lot is assessed based on AQC sampling and testing
(using defined AQC acceptance procedures) of the as-constructed
pavement.
As-Designed Lot Life-Cycle Cost (LCCDES):
The estimated post-construction LCC used to represent the
as-designed pavement quality. This value is based on the as-designed AQC
target values (means and standard deviations) selected by the
agency.
As-Designed Pavement: The desired concrete
pavement, as defined by the agency. The desired quality level of the
pavement is specified in terms of target as-designed AQC means and
standard deviations.
Buyer: That organization or entity
ultimately responsible for the purchase of the materials and work
required for the completion of a highway or transportation contract. May
be used interchangeably with the terms agency, purchaser,
consumer, or owner.(9)
Constant
Values: Project-specific variables required by the distress
indicator and cost models that do not differ between the as-designed and
as-constructed pavements. These variables define many of the pavement's
characteristics and can be grouped into general categories such as
traffic, project location and description, climatic conditions, slab
design and support, load transfer, and M & R unit
costs.
Construction Pass: The defining width of an ongoing
paving operation. This definition is used since the width of paving may
consist of more than one traffic lane.
Discount Rate: Used
to translate actual LCC's into equivalent present worth costs. It is
estimated as the difference between the interest and inflation rates
over a long time period, representing the real value of money over time.
The interest rate, often referred to as the market interest rate,
is associated with the cost of borrowing money and represents the
earning power of money.(10) The inflation rate is typically
defined as the rate of increase in the prices of goods and services
(construction of highways) and represents changes in the purchasing
power of money.(10)
Distress Indicator: A
measure of the condition of an existing pavement section at a particular
point in time.(4) These key pavement distresses are used to
define pavement performance. Distress indicators included in the current
PRS approach include transverse slab cracking, transverse joint
faulting, transverse joint spalling, and pavement smoothness over time.
Within the PRS, the distress indicators are predicted (over a chosen
analysis period) using the best available empirical or mechanistic
models. Model inputs include project-specific constant values and
representative mean values of the selected AQC's.
Equivalent
Single-Axle Load (ESAL): An 80-kN single-axle traffic loading. The
ESAL is the standard traffic measure used by most SHA's and design
methods. Average daily traffic (ADT) numbers are translated into
equivalent ESAL's. Many of the distress indicator models are functions
of the cumulative ESAL's applied over the chosen analysis
life.(11)
Expected Pay (EP) Curve: A graphic
representation of an acceptance plan that shows the relation between the
actual quality of a lot and its expected pay (i.e., mathematical pay
expectation, or the average pay the contractor can expect to receive
over the long run for submitted lots of a given
quality).(4)
Global Rehabilitation Activities:
Rehabilitation activities applied to the entire lot at one time in
response to declining global pavement conditions. These
activities are specifically applied to address pavement condition
indicators such as decreasing pavement smoothness, increasing amounts of
localized distress, or increasing amounts of applied localized
rehabilitation. Trigger values for these pavement condition indicators
must be selected to determine the timing of a global rehabilitation.
Examples of global rehabilitation activities include AC overlays, PCC
overlays, and diamond grinding.
In Situ Sampling: AQC
sampling procedures in which samples are taken ULectly from or on the
in-place concrete pavement (e.g., cores and surface profile
measurement).
Initial Design Life: Amount of time for
which the chosen pavement design is expected to carry traffic loads
without the application of a global rehabilitation (AC overlay, PCC
overlay, diamond grinding).
International Roughness Index
(IRI): The IRI is based on simulation of the roughness response of a
car traveling at 80 km/h. It is a ratio of the accumulated suspension
motion of the car divided by the distance traveled. The scale ranges
from 0 (perfectly smooth surface) to 20,000 mm/km, with larger values
indicating greater roughness. A value of 3,000 mm/km is often considered
to be the breaking point between "rough" and "smooth" pavements on
high-speed highways.
Jointed Plain Concrete Pavement (JPCP):
A PCC pavement type characterized by short joint spacing (less than
6 m) and no reinforcing steel mesh or bars. JPCP pavements may or may
not be constructed with dowels at the transverse joints. These pavements
typically include tie bars at longitudinal joints. Slab thicknesses for
this pavement type have historically ranged from 152 to 254 mm; however,
newer pavements are being constructed with thicknesses of 305 mm or
more.
Life-Cycle Cost (LCC): The estimated cumulative
present worth cost of a pavement lot over a specified analysis period.
The LCC, as used in PRS, may include estimated future maintenance,
rehabilitation, and user costs over a chosen analysis period. The
initial construction cost is not included in the LCC since it is
identical for both the as-designed and the as-constructed pavements. LCC
values are expressed in units of present worth dollars (PW$) per
kilometer.
Localized Rehabilitation Activities:
Rehabilitation activities that may be used to correct
localized pavement distresses. Localized distresses are defined
as those that may affect an individual joint (transverse joint spalling
and transverse joint faulting) or slab (transverse slab
cracking).
Lot: A discrete quantity of constructed
pavement to which an acceptance procedure (and corresponding pay
adjustment) is applied. All pavement placed within a lot should consist
of the same mix design and material sources, should be subjected to the
same support conditions (base type, base thickness, subbase type,
subbase thickness, subgrade treatment), and should consist of the same
design characteristics (joint spacing, drainage, shoulder type,
dowel-bar diameter, traffic, and AQC design values).
Lot
Length: Equal to one day's production or less. The minimum lot
length should not be less than 0.16 km. Any section of lesser length
will be added to the preceding lot or succeeding lot.
Lot
Width: The lot width is defined as the total width of pavement, one
or more traffic lanes, being placed at one time in the mainline paving
process. This paving width is also referred to as a construction
pass,since it describes the total width of pavement being placed in
one pass of the paving train. The entire width of a widened lane is
included; however, shoulders are to be excluded.
Maintenance
Activities: Routine activities performed as preventive measures.
This maintenance is typically applied at certain fixed intervals of time
over the life of a pavement lot (commonly on an annual basis). Examples
of maintenance activities include transverse crack and joint
sealing.
Maintenance and Rehabilitation (M & R) Plan:
The defined set of rules used to predict the type and timing of
future M & R activities. Expected localized and global
rehabilitation activities are determined based on chosen trigger values
applied to each distress indicator. Maintenance activities are applied
by defining the amount and application frequency (e.g., seal 100 percent
of the transverse joints every 2 years).
Maximum Quality Limit
(MQL): Agency-chosen maximum limit for acceptable AQC specimen
sample quality. If an AQC specimen sample value is measured to have
greater quality than the defined MQL, the representative specimen sample
value (used in the acceptance procedures) is set equal to the defined
MQL (i.e., the contractor does not receive credit for quality provided
in excess of the MQL). For concrete strength, slab thickness, entrained
air content, and percent consolidation around dowels, better quality
than the MQL is identified by specimen sample values greater than
the MQL; however, for initial smoothness, better quality than the MQL is
identified by specimen sample values less than the
MQL.
Nondestructive Testing: AQC sampling and testing
methods conducted on the in-place pavement, without disturbing the
pavement's structural integrity or surface characteristics.
Operating Characteristic (OC) Curve: A graphic
representation of an acceptance plan that shows the relationship between
the actual quality of a lot and the probability of its acceptance at
various payment levels.(4)
PaveSpec 2.0: The
revised PRS specification simulation software developed under this
research project. This software is used to demonstrate the PRS approach
by simulating pavement performance, determining corresponding LCC's,
generating preconstruction output, and computing pay adjustments. Its
specific functions are described in the PaveSpec 2.0
User Guide (appendix G, volume IV).
Pay Adjustment:
The actual pay adjustment (incentive or disincentive in PW$) for the
as-constructed lot. The computation of the lot pay adjustment differs
between the Level 1 and Level 2 PRS.
Level 1 Pay Adjustment—The Level 1 pay adjustment is
computed using the determined Level 1 lot composite pay factor (CPF).
The actual Level 1 lot pay adjustment is computed using the relationship
presented in equation 101-1.
PAYLOT = BID * (PFCOMPOSITE –
100) * LOTLENGTH
(101-1) where
PAYLOT = Adjusted payment paid to the
contractor for the as-constructed lot, $.
BID = Contractor bid price,
$/km.
PFCOMPOSITE = The determined Level 1 lot
CPF, percent (e.g., 101 percent is expressed as
101.0).
LOTLENGTH = Measured actual
as-constructed lot length, km.
Level 2 Pay Adjustment—The Level 2 pay adjustment is
computed using the determined Level 2 lot pay factor. The actual Level 2
lot pay adjustment is computed using the relationship presented in
equation 101-2.
PAYLOT = BID * (PFLOT – 100) *
LOTLENGTH
(101-2) where
PAYLOT = Adjusted payment paid to the
contractor for the as-constructed lot, $.
BID= Contractor bid
price, $/km.
PFLOT = The determined Level 2
overall lot pay factor, percent (e.g., 101 percent is expressed as
101.0).
LOTLENGTH = Measured actual
as-constructed lot length, km.
Pay Factor (PF): The percent of the bid price that the
contractor is paid for the construction of a concrete pavement lot.
There are a number of different pay factor-related definitions used
within this report.
Basic Pay Factor Definition—The underlying equation
used to compute a pay factor for a given lot (based on the comparison of
LCC's) is presented as equation 101-3. This equation is used to compute
the pay factor for each simulated lot.
PFLOT = 100 * (BID + [LCCDES
– LCCCON])/BID
(101-3) where
PFLOT = Overall pay factor for the
as-constructed lot, percent.
BID = Representative
contractor's unit bid price for the lot,
$/km.
LCCDES = As-designed life-cycle unit
cost for the lot (computed using target AQC's),
PW$/km.
LCCCON = As-constructed life-cycle unit
cost for the lot (computed using AQC test results from the
as-constructed lot), PW$/km.
Level 1 Individual AQC Pay Factors—The pay factors
(associated with the measured AQC's) computed using the developed Level
1 individual AQC pay factor equations. Each Level 1 AQC pay factor
(expressed as a percentage) is a function of the measured as-constructed
AQC lot mean and standard deviation. (Note: Level 1 individual AQC pay
factor equations are based on data simulated using the PaveSpec 2.0
computer software.) The final Level 1 individual AQC pay factors may be
limited to agency-chosen pay factor practical limits.
Level 1
Composite Pay Factor—The overall pay factor (expressed as a
percentage) for an as-constructed lot computed using a Level 1
specification. This pay factor is determined using the agency-defined
CPF equation (a simple mathematical function of the individual Level 1
AQC pay factors). The final Level 1 lot CPF (which may be limited to
agency-chosen pay factor practical limits) is used to determine the
contractor's Level 1 lot pay adjustment.
Level 2 Pay
Factor—The overall pay factor (expressed as a percentage) for an
as-constructed lot computed using a Level 2 specification. This pay
factor is computed using equation 101-3 and may be limited to
agency-chosen pay factor practical limits. The PaveSpec 2.0 computer
software is used to simulate the required LCCDES based on
SHA-defined AQC target values, and estimate the LCCCON based
on the measured as-constructed AQC samples.
Performance-Related Specifications (PRS): Construction
specifications placed on key materials and construction AQC's (e.g.,
concrete strength, slab thickness) that have been demonstrated to
correlate strongly with long-term pavement performance. These
specifications are based on quantified relationships (or mathematical
models) that relate measured AQC's to subsequent pavement performance
and the corresponding costs.
Present Serviceability Rating
(PSR): An indicator of pavement smoothness based on the subjective
ratings of users. The PSR is expressed as a number between 0 and 5 with
the smaller values indicating greater pavement roughness. The scale is
translated into general pavement condition description categories using
the following translations.(11)
0 – 1 Very
poor.
1 – 2
Poor.
2 – 3
Fair.
3 – 4
Good.
4 – 5 Very
good.
Present Worth (PW) Method: A discounted cash flow analysis
that involves the conversion of all of the present and future costs to a
base of today's costs.(10) Expected future costs are
translated into equivalent present worth costs using equation 101-4.
PWCOST = C / (1 + i)T
(101-4)
where
PWCOST = Present worth of yearly cost
(C).
C = M & R, or user cost incurred during year
T.
T = Year during which the observed cost (C) was
incurred.
i = Chosen discount
rate.
Quality Assurance (QA): All those planned and systematic
actions necessary to provide adequate confidence that a product or
service will satisfy given requirements of quality. Within an
organization, QA serves as a management tool. In contractual situations,
QA serves to provide confidence in the
supplier.(9)
Quality Control (QC): The sum
total of activities performed by the seller (producer, manufacturer, or
contractor) to make sure that a product meets contract specification
requirements. Within the context of highway construction, QC includes
materials handling and construction procedures; calibration and
maintenance of equipment; production process control; and any sampling,
testing, and inspection done for these
purposes.(9)
Rejectable Quality Limit (RQL):
Agency-chosen mimimum limit for acceptable AQC specimen sample
quality. If an AQC specimen sample value is measured to have poorer
quality than the defined RQL, AQC retesting procedures will apply. For
concrete strength, slab thickness, entrained air content, and percent
consolidation around dowels, poorer quality than the RQL is identified
by specimen sample values less than the RQL; however, for initial
smoothness, poorer quality than the RQL is identified by specimen sample
values greater than the RQL.
Sample Mean: The
average of n random AQC sample values. This sample mean is computed
using equation 101-5.
MEANSAMPLES = å(xi) /n
(101-5) where
MEANSAMPLES = The computed mean of
n random AQC samples.
xi = 1 to n
random sample values.
n = Total number of random
samples.
(Note: If m replicate samples are taken from each sampling
location, the mean of each set of m test results is used to
define a random sample value.)
Sample Standard Deviation:
An estimate of the true population standard deviation, s. If this estimate is to be unbiased, a correction
factor must be applied. This unbiased sample standard deviation is
computed using equation 101-6.
SDSAMPLES = ({[å(xi
–MEANSAMPLES)2] /(n –
1)}/m)0.5 / CSD
(101-6) where
SDSAMPLES = The computed unbiased
standard deviation of all of the random sample
values.
MEANSAMPLES = The computed mean of all
of the random sample values.
n = Total number of
random samples.
xi = 1
to n sample values.
m = The number of
replicate specimen test results used to compute one sample
value.
CSD = Correction factor based on the
total sample size, n, used to obtain unbiased estimates of the actual
lot sample standard deviation, s. Appropriate
CSD values are determined using table
PRS-101-01.
Table
PRS-101-01. Correction factors used to obtain unbiased estimates of the
actual standard deviation.
Number of Sample Values, n |
Correction Factor, CSD |
2 |
0.7979 |
3 |
0.8862 |
4 |
0.9213 |
5 |
0.9399 |
6 |
0.9515 |
7 |
0.9594 |
8 |
0.9650 |
9 |
0.9693 |
10 |
0.9726 |
30 |
0.9915 |
50 |
0.9949 |
Note: Unbiased estimates of the standard
deviation are automatically calculated and used in the determination of
lot pay factors within PaveSpec 2.0.
Sample Value:
An AQC value used to represent one sample location within a sublot.
A representative sample value may be the ULect measured value from one
test taken at a sample location (no replicate test result values, i.e.,
m =1), or equal to the mean of m replicate test result
values (from m replicate tests) taken at the same sample
location.
Seller: Any entity providing materials and work
required for the completion of highway or transportation work. This
includes the contractor and all subcontractors. The term may be used
interchangeably with producer or
supplier.(9)
Sublot: A portion of a lot.
Each lot is divided into sublots of approximately equal surface area.
Sublot lengths are selected so that one or more samples may be taken
from each sublot for each considered AQC. The minimum sublot length
cannot be less than 0.16 km (to accommodate the measurement of initial
smoothness). Any section of lesser length will be added to the preceding
sublot. Note that in PRS, measurements for all AQC's must be obtained
from each sublot so that performance can be predicted.
Target
Sublot Length: The chosen default linear length for each sublot.
Each as-constructed sublot should initially be assumed to be equal to
this target sublot length.
Test Result Value: The computed
AQC value from one AQC test. For concrete strength, slab thickness, and
entrained air content, this is the testing result from one specimen. For
initial smoothness, this is the value obtained from one pass of the
profilograph. For percent consolidation around dowels, this is the value
obtained from one relative density comparison.
Section PRS-110.
Quality Assurance |
 |
 |
PRS–110.01
Samples, Tests, and Referenced Specifications. The contractor
shall be responsible for the quality of the construction and materials
incorporated into the contract. The contractor shall perform all necessary
QC inspection, sampling, and testing. All materials will be approved for
acceptance through the agency's acceptance procedures. The agency is
responsible for determining the acceptability of the construction and
materials incorporated therein. The agency may use the results of the
contractor's inspection, sampling, and testing as a part of its acceptance
procedures, provided the contractor has an approved QC program.
PRS–110.02 Qualified
Testing Laboratory. The agency central laboratory shall be
accredited by the AASHTO Accreditation Program (AAP). All testing
laboratories (agency, contractor, consultant, or vendor) shall be approved
by the agency.
The contractor's QC laboratory shall be furnished
and maintained with adequate ventilation, heat, light, water, sink and
drainage, electrical or gas outlets (or both), work tables, shelves, and
supply cabinets. The laboratory shall be supplied with equipment and
materials necessary to perform all tests required by these specifications
and shall be maintained in such condition that the equipment will meet the
applicable requirements of the agency. (The agency may want to list the
specific equipment that is deemed necessary to satisfy the QC testing
requirements of the applicable specifications.)
PRS–110.03 Technician
Certification. The agency shall require that individuals who
perform one or more of the actual sampling, testing, and inspection
functions for the agency, contractor, vendor, or private laboratories be
certified.
Certified sampling and testing personnel provide added
assurances that the sampling and testing will be performed correctly and
that the results will be valid. The certification program recognized by
the agency should be one or more of the following:
- National Institute for Certification in Engineering Technologies.
- The American Concrete Institute or other trade association.
- Individually developed agency program.
- Reciprocity between agencies.
For additional information concerning technician certification, see the
"Sampling and Testing Personnel" section of the 1996 AASHTO
Implementation Manual for Quality
Assurance.(28)
PRS–110.04 Quality Control.
The contractor shall provide and maintain a QC system that will assure all
materials and products submitted to the agency for acceptance will conform
to the contract requirements, whether manufactured or processed by the
contractor or procured from suppliers, subcontractors, or vendors. The
contractor shall perform, or have performed, the inspections and tests
required to substantiate product conformance to contract document
requirements. The contractor shall also perform, or have performed, all
inspections and tests otherwise required by the contract. The contractor's
QC inspections and tests shall be documented and provided to the agency.
The contractor shall maintain adequate records of all inspections and
tests. The records shall include the nature, number, and type of
deficiencies found; the quantities rejected by the contractor; and the
nature of corrective action taken, as appropriate. The contractor shall
maintain standard equipment and qualified personnel as required by the
specifications to assure conformance to contract requirements. Procedures
will be subject to approval by the agency before the work is
started.
The contractor shall prepare a QC plan detailing the type
and frequency of inspection, sampling, and testing deemed necessary to
measure and control the various properties of materials and construction
governed by the specifications. The QC plan shall be submitted in writing
to the agency at the preconstruction conference. This plan shall include
the following:
- Construction items covered by the plan.
- Tests to be performed.
- Testing frequencies.
- Sampling locations and techniques.
- Documentation procedures, including:
- Inspection and test records.
- Temperature measurements.
- Accuracy, calibration, or recalibration checks performed on
production or testing equipment.
- Control charts.
The plan shall identify the personnel responsible for the contractor's
QC. This should include the name of the company official who will act as a
liaison with agency personnel and the names of the certified technicians
who will ULect and conduct the inspection program. When required in these
specifications, the contractor shall provide a testing facility or
laboratory.
Note: The agency should publish, as a separate
document, the minimum content of an acceptable QC plan. Examples of
minimum content of an acceptable QC plan are provided in the following
publications:
- Appendix A—Guide for Quality Control and Acceptance
Requirements for Portland Cement Concrete from the 1996 AASHTO
Quality Assurance Guide Specification.(9)
- Appendix D—Quality Control Plans from the 1996 AASHTO
Implementation Manual for Quality Assurance.(28)
PRS–110.05 Acceptance. The
agency is responsible for determining the acceptability of the material
produced. Acceptance of the material is based on the inspection of the
construction, monitoring of the contractor's QC program, and acceptance
test results.
- Sampling and Testing. The acceptance sampling and testing is
the responsibility of the agency. The contractor must provide the
necessary materials for testing.
The agency may use the
contractor's QC test results as a part of the acceptance procedures,
provided:
- The agency's inspection and monitoring activities indicate the
contractor has followed the approved QC plan, and
- The results from the contractor's QC sampling and testing
compare favorably with the agency's results in accordance with
Section PRS–110.05 (B).
- Validation Procedures for QC Test Results. If the agency is
to use the contractor's QC test data, the contractor's test results
shall be validated in accordance with appendix F or appendix G of the
1996 AASHTO Implementation Manual for Quality
Assurance.(28) The appropriate level of significance is
left to the agency's discretion.
PRS–110.06 Quality Pay
Adjustments. The lot pay adjustment provisions shall be developed
based on the quality of those AQC's chosen by the agency for acceptance
under the specifications. The agency will determine lot pay adjustments
based on the measured AQC sample and testing results, in accordance with
the developed pay adjustment provisions. The contractor shall be paid the
amount of the computed adjusted pay on a lot-by-lot basis.
PRS–110.07 Dispute
Resolution. When there are significant discrepancies between the
agency's and contractor's test results, dispute resolution procedures will
be used.
- Procedures for Resolving Differences. The contractor and
agency must agree upon the test methods to be used. If the test method
is not in question, then the agency and contractor should look for
differences in procedures and correct the inappropriate procedure before
moving to third-party resolution.
- Third Party Resolution. The agency's central laboratory or an
independent laboratory will be used to determine material quality
results. Whichever laboratory is used, it should be AAP accredited and
the results shall be binding.
The contractor will be responsible for the cost associated with the
third-party resolution if the final result indicates that the agency's
acceptance test results were correct. Likewise, the agency will be
responsible for the cost when the final result indicates that the
contractor's acceptance test results were correct. For additional
information, see the "Dispute Resolution" section of the 1996 AASHTO
Implementation Manual for Quality Assurance. (28)
DIVISION 500. RIGID
PAVEMENT
Section PRS–501.
Jointed Plain Cement Concrete
Pavement |
 |
 |
PRS–501.01 Description.
This work shall consist of constructing a JPCP on a prepared subgrade or
base course, in accordance with these specifications. These specifications
apply only to the PCC pavement slab placed in the traffic lanes, and
specifically address the following: materials, construction requirements,
method of measurement, basis of acceptance, and basis of payment. Pavement
shoulders are not addressed under these specifications and shall be
accepted using conventional acceptance procedures.
The pavement
project is divided into one or more lots for acceptance purposes. Each
defined lot will be accepted independently based on AQC sampling and
testing conducted by the agency. The contractor shall receive 100 percent
of the bid price for a lot if the quality of construction exactly equals
that of the target as-designed pavement parameters (AQC target means and
standard deviations). If the quality of construction for a lot exceeds or
is below the target as-designed AQC's, the contractor shall receive a pay
adjustment for the lot (incentive or disincentive). The amount of the pay
adjustment is determined based on a comparison of the estimated
post-construction LCC's determined independently for both the as-designed
and as-constructed pavements. All calculations for the LCC-based pay
adjustments shall be performed using the PaveSpec 2.0 computer
software.
PRS–501.02
Materials. Materials shall meet the provisions of the following
subsections included in the 1993 AASHTO Guide Specifications for
Highway Construction.(29)
- Portland cement 701.01
- Fine aggregate 703.01
- Coarse aggregate 703.01
- Joint filler 707.01
- Reinforcing steel 711.01
- Curing materials 713.01
- Air-entraining admixtures 713.02
- Chemical admixtures 713.03
- Water 714.01
- Fly ash (optional) 714.11
- Ground granulated blast-furnace slag
714.12
PRS–501.03
Construction Requirements. Agency specifications for construction
requirements, including contractor process control, shall be placed
here.
PRS–501.04 Methods of AQC
Measurement.
- Lots. Each discrete quantity of
pavement representing an as-constructed lot shall be accepted
independently by the agency. The length of each lot shall be defined as
equal to one day's production or less. It is recommended that a lot
length always be set equal to the entire day's production unless a
significant within-day change occurs in the paving operation (e.g.,
change in aggregate source, stoppage of the paving operations for a
significant amount of time). When applicable, the entire width of a
widened traffic lane is to be considered part of the mainline
paving.Pavement shoulders are not included as part of a lot.
- Sublots. The agency shall attempt to
divide each as-constructed lot into sublots with lengths equal to the
target sublot length. The target sublot length shall be defined by the
agency in accordance with the guidelines set forth in chapter 5 of this
volume. The length of the last paved sublot within a lot shall be
determined in accordance with the guidelines set forth in chapter 5 of
this volume. The total number of sublots observed in an as-constructed
lot shall be used as the representative number of sublots per lot for
the given lot. The width of a sublot is defined by the width of the lot
in which the sublot is observed.
If the final total lot length is
less than the agency-chosen target sublot length, the lot may be
accepted by the engineer upon a visual inspection of the section and a
review of process control results. The agency also has the option to add
this material to that of the preceding or succeeding lot.
- Definition of
Pavement Performance. The agency shall define future pavement
performance in terms of any or all of the following distress indicators:
- Transverse Joint Spalling.
- Transverse Joint Faulting.
- Transverse Slab Cracking.
- Pavement Smoothness Over Time (expressed in terms of PSR or
IRI).
The definition of pavement performance shall be
made in accordance with the guidelines set forth in chapter 5 of this
volume.
- Included
Acceptance Quality Characteristics. The agency shall base the
acceptance of an as-constructed pavement lot on any or all of the
following AQC's:
- Concrete strength.
- Slab thickness.
- Entrained air content.
- Initial smoothness.
- Percent consolidation around dowels.
The selection
of included AQC's shall be accomplished in accordance with the
guidelines set forth in chapter 5 of this volume.
- Selection of AQC
Target Values. The agency shall define the desired AQC lot
quality in terms of AQC means and standard deviations (target values).
Target values shall be identified for each of the AQC's chosen to be
included in the specifications. The specific chosen target values are
also dependent on the chosen AQC sampling and testing methods. The
selection of AQC target values shall be accomplished in accordance with
the guidelines set forth in chapter 5 of this volume.
- Identification of
AQC Limits for Acceptance. The agency shall define practical
maximum and minimum quality limits to be applied to each measured
specimen sample value. The maximum limit shall be referred to as the
Maximum Quality Limit (MQL), and the minimum limit shall be referred to
as the Rejectable Quality Limit (RQL). If the specimen sample value is
measured to be of poorer quality than the defined RQL, then retesting
procedures shall be applied. If the specimen sample value is measured to
be of greater quality than the defined MQL, the representative specimen
sample value (used in the acceptance procedures) shall be set equal to
the defined MQL (i.e., the contractor shall not receive credit for
quality provided in excess of the MQL). The selection of AQC limits (RQL
and MQL) shall be accomplished in accordance with the guidelines set
forth in chapter 5 of this volume.
- AQC Sampling and
Testing Methods. Acceptance of an as-constructed pavement lot is
based on the sampling and testing of key AQC's. Only those AQC's
selected by the agency for inclusion in the specifications are to be
sampled. AQC samples shall be taken from every sublot within a given lot
using agency-defined sampling frequencies (the number of samples per
sublot may differ for each included AQC). The number of AQC sampling
locations per sublot, and their corresponding random sampling locations
within each sublot, shall be determined in accordance with the
guidelines set forth in chapter 5 of this volume.
The acceptance
sampling and testing for each included AQC shall be conducted using one
of the agency preapproved methods that follow. All AQC acceptance
sampling shall be performed in accordance with the following standard
specifications:
- American Association of State Highway and Transportation
Officials, Standard Specifications for Transportation Materials and
Methods of Sampling and Testing, Part II
Tests.(19)
- American Society for Testing and Materials (ASTM),
Annual Book of ASTM Standards, Section 4, Construction, Road
and Paving Materials.(20)
All AQC acceptance and testing shall be conducted in accordance with
the guidelines set forth in section PRS–110.05,
Acceptance.
- Concrete Strength. The
28-day flexural strength (third-point loading—28-day modulus of rupture
[M R ]) is required for the acceptance of concrete strength.
Specific 28-day MR values representing each sublot sample
location shall be determined using the concrete strength sampling and
testing procedures defined below.
- Sampling of
Concrete Strength. Samples used in the determination of the
28-day M R shall consist of one of three methods. [The
agency shall select one of the following.]
- Beams. Beam specimens
(with agency-specified dimensions) are to be molded, handled, and
cured in accordance with AASHTO T-23, Making and Curing Concrete
Test Specimens in the Field.(19) Beam specimens for
each sublot shall be made with plastic concrete taken from in front
of the paver at predetermined random longitudinal sampling
locations. Random longitudinal sampling locations shall be
identified in accordance with the guidelines set forth in chapter 5
of this volume. The number of beam specimens per sampling location
(replicate specimens) and the number of sampling locations per
sublot shall be defined by the agency in accordance with the
guidelines set forth in chapter 5 of this volume.
- Cylinders. Cylinder
specimens shall be molded, handled, and cured in accordance with
AASHTO T-23, Making and Curing Concrete Test Specimens in the
Field.(19) All cylinder specimens shall be cast in
molds with a nominal length-to-diameter ratio of 2. An appropriate
cylinder specimen diameter shall be determined based on the
following:
- A minimum 102-mm cylinder diameter shall be used when the
maximum aggregate size is 32 mm or less.
- A minimum 152-mm cylinder diameter shall be used when the
maximum aggregate size is greater than 32 mm.
Cylinder
specimens for each sublot shall be made with plastic concrete taken
from in front of the paver at predetermined random longitudinal
sampling locations. Random longitudinal sampling locations shall be
determined in accordance with the guidelines set forth in chapter 5
of this volume. The number of cylinder specimens per sampling
location (replicate specimens) and the number of sampling locations
per sublot shall be defined by the agency in accordance with the
guidelines set forth in chapter 5 of this volume.
- Cores. Core specimens shall
be extracted from the hardened pavement slab between 48 and 72 hours
after placement, in accordance with AASHTO T-24, Obtaining and
Testing Drilled Cores and Sawed Beams of Concrete.
(19) Core specimens shall be extracted from the hardened
concrete slab at predetermined random sampling locations. Random
core locations shall be determined in accordance with the guidelines
set forth in chapter 5 of this volume. The number of core specimens
per sublot shall be defined by the agency in accordance with the
guidelines set forth in chapter 5 of this volume.
An
appropriate core specimen diameter shall be determined based on the
following:
- A minimum 102-mm diameter shall be used when the maximum
aggregate size is 32 mm or less.
- A minimum 152-mm diameter shall be used when the maximum
aggregate size is greater than 32 mm.
Prior to
testing, all core specimens shall be trimmed to a nominal
length-to-diameter ratio of 2. A correction factor shall be applied
(in accordance with AASHTO T-24, Obtaining and Testing Drilled
Cores and Sawed Beams of Concrete) to cores having a
length-to-diameter ratio of less than 1.94, whereas cores having a
length-to-diameter ratio between 1.94 and 2.10 require no such
correction.(19) Cores with a length-to-diameter ratio
exceeding 2.10 shall be reduced in length to fall within the ratio
limits of 1.94 to 2.10.
- Timing of
Concrete Strength Testing. The agency shall define the timing
of the concrete strength specimen testing to be used in estimating the
28-day (equivalent 28-day laboratory maturity) flexural strength
(third-point loading) of the as-constructed pavement. Each specimen
(molded beam, molded cylinder, or extracted core) shall be tested
independently and translated (if necessary) into an M R at
an equivalent 28-day laboratory maturity.
The timing of
concrete strength specimen testing shall be defined by the agency and
expressed in terms of an equivalent laboratory maturity. The
agency-chosen timing of concrete strength specimen testing shall meet
the following requirements:
- Testing shall not be conducted until the specimen achieves a
maturity of at least 72 hours (3 days) of the equivalent laboratory
curing condition maturity.
- Testing must be conducted at or before the point when the
specimen achieves a maturity equal to 672 hours (28 days) of the
equivalent laboratory curing condition maturity.
- Testing-Related
Procedures (Conducted Prior to Specimen Testing). The agency
shall perform the following testing-related laboratory and field
procedures (as required) in preparation for concrete strength specimen
testing.
- Laboratory
Maturity Calibration. Prior to the placement of any
as-constructed concrete pavement, the agency shall develop required
mix-specific maturity curves in the laboratory. The representative
maturity curves (expressed as flexural, compressive, or
split-tensile strength versus maturity) shall be determined using
the Arrhenius maturity method, and in accordance with ASTM C-1074,
Standard Practice for Estimating Concrete Strength by the
Maturity Method, and the guidelines set forth in chapter 5 of
this volume.(20)The required developed maturity curves
(and corresponding equations) shall be included as Series
A attachments to these specifications. This laboratory
maturity calibration is only required if sample testing is conducted
when the equivalent laboratory maturity is less than 28
days.
- Laboratory-Developed
Inter-Strength Relationships. Prior to the placement of any
as-constructed pavement, the agency shall develop required
mix-specific inter-strength relationships (i.e., compressive
strength to flexural strength, or split-tensile to flexural strength
relationships) in the laboratory. These relationships (curves and
respective equations) shall be developed in accordance with the
guidelines set forth in chapter 5 of this volume. The required
inter-strength relationships (curves and equations) shall be
included as Series
B attachments to these specifications.
- Measuring
Maturity in the As-Constructed Pavement. If the agency
selects core specimens as the sampling type, the maturity of the
as-constructed pavement shall be monitored for each sublot.
Temperatures shall be measured at one central location per sublot
using a thermocouple placed at mid-depth of the pavement slab (the
thermocouple shall be embedded into the pavement using an
agency-approved method). The thermocouple shall be connected to an
agency-approved maturity meter. The maturity meter shall begin
recording pavement temperatures at the time when the thermocouple
becomes completely covered with concrete. Temperatures shall be
measured for a given sublot until all of the cores representing the
sublot are extracted from the as-constructed pavement.
- Specific
Concrete Strength Testing Procedures. Representative flexural
strength (third-point loading) values, at a 28-day equivalent
laboratory maturity, shall be determined for each specimen using one
of three specific testing procedures. [The agency shall select one of
the following.]
- Flexural Testing of
Beams—If the concrete strength of the as-constructed
pavement is to be evaluated using beam specimens tested in flexural
strength (third-point loading), then the following procedure shall
apply.
- Each beam specimen shall be tested (at an agency-defined
equivalent laboratory maturity) for flexural strength (third-point
loading) in accordance with AASHTO T-97, Flexural Strength of
Concrete (Using Simple Beam With Third-Point
Loading).(19)
- Each testing result shall be translated to a 28-day flexural
strength (28-day equivalent laboratory maturity) using the
attached mix-specific flexural strength (third-point loading)
versus maturity curve and equation, in accordance with the
guidelines set forth in chapter 5 of this volume.; The required
maturity curve shall be included as a Series
A attachment to these specifications. No maturity
translations need be applied if beam specimens are tested directly
at a 28-day equivalent laboratory maturity.
- Compression
Testing of Cylinders or Cores—If the concrete strength of
the as-constructed pavement is to be estimated using cylinder or
core specimens tested in compression strength, then the following
procedure shall apply.
- Each core specimen shall be tested (at an agency-defined
equivalent laboratory maturity) for compressive strength in
accordance with AASHTO T-24, Obtaining and Testing Drilled
Cores and Sawed Beams of Concrete.(19) Each
cylinder specimen shall be tested (at an agency-defined equivalent
laboratory maturity) for compressive strength in accordance with
AASHTO T-22, Compressive Strength of Cylindrical Concrete
Specimens.(19)
- Each testing result shall be translated to a 28-day
compressive strength (28-day equivalent laboratory maturity) using
the attached mix-specific compressive strength versus maturity
curve and equation, in accordance with the guidelines set forth in
chapter 5 of this volume. The required maturity curve shall be
included as a Series
A attachment to these specifications. No maturity
translations need be applied if cylinder or core specimens are
tested directly at a 28-day equivalent laboratory
maturity.
- Each estimated core or cylinder compressive strength (at a
28-day equivalent laboratory maturity) shall be translated into a
representative 28-day flexural strength using the attached
mix-specific compressive strength to flexural strength
inter-strength relationship (curve and corresponding equation).
The required inter-strength relationship shall be included as a Series
B attachment to these specifications.
- Split-Tensile
Testing of Cylinders or Cores—If the concrete strength of
the as-constructed pavement is to be estimated using cylinder or
core specimens tested in split-tensile strength, then the following
procedures shall apply.
- Each core specimen shall be tested (at an agency-defined
equivalent laboratory maturity) for split-tensile strength in
accordance with AASHTO T-24, Obtaining and Testing Drilled
Cores and Sawed Beams of Concrete.(19) Each
cylinder specimen shall be tested (at an agency-defined equivalent
laboratory maturity) for split-tensile strength in accordance with
AASHTO T-198, Splitting Tensile Strength of Cylindrical
Concrete Specimens.(19)
- Each testing result shall be translated to a 28-day
split-tensile strength (28-day equivalent laboratory maturity)
using the attached mix-specific split-tensile strength versus
maturity curve and equation, in accordance with the guidelines set
forth in chapter 5 of this volume. The required maturity curve
shall be included as a Series
A attachment to these specifications. No maturity
translations need be applied if cylinder or core specimens are
tested directly at a 28-day equivalent laboratory
maturity.
- Each estimated core or cylinder split-tensile strength result
(at a 28-day equivalent laboratory maturity) shall be translated
into a representative 28-day flexural strength using the attached
mix-specific split-tensile strength to flexural strength
inter-strength relationship (curve and corresponding equation).
The required inter-strength relationship shall be included as a Series
B attachment to these specifications.
- Concrete Strength
Acceptance. The contractor shall furnish paving equipment and
employ methods that give the contractor the ability to produce
concrete strengths that meet, or better, the agency-defined target
concrete strength quality. The agency-desired target concrete strength
quality is defined as the mean and standard deviation of the
representative concrete strength values computed for a given lot.
Representative concrete strength values are determined for each sample
location within each sublot (average of replicates within a sampling
location). The agency-defined target concrete strength shall be
defined in table
PRS-501-01 of these specifications. An as-constructed lot with a
concrete strength quality that differs from the target concrete
strength quality shall be accepted with price adjustments (incentive
or disincentive).
View Table PRS-501-01. Agency-Chosen AQC
Sampling and Testing Methods, and Target Values.
Representative 28-day flexural strength values shall be
determined for each specimen using one of the methods described above.
The agency shall define AQC limits (RQL and MQL) to be applied to each
specimen value within a sublot. The following procedure shall apply:
- If a specimen strength value is less than the defined RQL, the
agency shall begin retesting procedures. Concrete strength retesting
procedures are specified in section PRS–501.05,
Methods of AQC Retesting.
- If a specimen strength value is greater than the defined MQL,
the measured specimen strength value shall be reduced to be equal to
the chosen MQL. The reduced specimen strength value shall be used
for acceptance.
- All specimen strength values greater than or equal to the RQL,
and less than or equal to the MQL, shall be used directly for
acceptance.
The specimen strength values (including
any adjustments) are then averaged within each sampling location to
give strength values representative of each sampling location. These
sampling location strength values (averages of replicate specimens)
are then used in the PaveSpec 2.0 computer software for the acceptance
of concrete strength. (Note: The strength value typically referred to
as a sample per sublot is actually the average value of all of
the replicate specimen values at that particular location).
- Slab Thickness
- Sampling
and Testing of Slab Thickness. The thickness of the
as-constructed slab shall be determined by measurements taken on cores
extracted from each sublot making up an as-constructed pavement lot.
Core specimens shall be extracted from the hardened concrete slab
between 48 and 72 hours after placement, in accordance with AASHTO
T-24, Obtaining and Testing Drilled Cores and Sawed Beams of
Concrete.(19) All cores used for the acceptance of slab
thickness shall have a minimum diameter of 102 mm.
Slab
thickness shall be measured on all cores extracted for the evaluation
of concrete strength; these measured values shall be used in lieu of
extracting additional slab thickness cores. When required, randomly
selected slab thickness core locations (independent of any cores taken
for the evaluation of concrete strength) shall be determined in
accordance with the guidelines set forth in chapter 5 of this volume. The number of slab thickness
core specimens per sublot shall be defined by the agency in accordance
with the guidelines set forth in chapter 5 of this volume.
The representative
thickness of each core shall be determined in accordance with AASHTO
T-148, Measuring Length of Drilled Concrete
Cores.(19)
- Slab Thickness
Acceptance. The contractor shall furnish paving equipment and
employ methods that give the contractor the ability to produce slab
thickness that meet, or better, the agency-defined target slab
thickness quality. The agency-desired target slab thickness quality is
defined as the mean and standard deviation of the slab thickness
values measured for a given lot. The agency-defined target slab
thickness shall be defined in table
PRS-501-01 of these specifications. An as-constructed lot with a
slab thickness quality that differs from the target slab thickness
quality shall be accepted with price adjustments (incentive or
disincentive).
The agency shall define AQC limits (RQL and MQL)
to be applied to each specimen value within a sublot. The following
procedure shall apply:
- If a specimen slab thickness value is less than the defined RQL,
the agency shall begin retesting procedures. Slab thickness
retesting procedures are specified in section PRS–501.05,
Methods of AQC Retesting.
- If a specimen slab thickness value is greater than the defined
MQL, the measured specimen slab thickness value shall be reduced to
be equal to the chosen MQL. The reduced specimen slab thickness
value shall be used for acceptance.
- All specimen slab thickness values greater than or equal to the
RQL, and less than or equal to the MQL, shall be used directly for
acceptance.
The specimen slab thickness values (including any
adjustments) are then used in the PaveSpec 2.0 computer software for
the acceptance of slab thickness.
- Entrained Air Content
- Sampling and
Testing of Entrained Air Content. The entrained air content of
the as-constructed pavement shall be determined using one of two
agency-approved sampling and testing methods. [The agency shall select
one of the following.]
- Pressure Meter
Tests of Plastic Concrete. Plastic concrete shall be taken
in front of or behind the paver at predetermined random longitudinal
sampling locations. Random longitudinal sampling locations shall be
identified in accordance with the guidelines set forth in chapter 5 of this volume. If beam or cylinder
specimens are required for the estimation of concrete strength,
entrained air content pressure meter tests may be conducted at the
same longitudinal locations used for the strength investigation. If
behind-the-paver samples are chosen, material shall be removed from
the slab using an agency-approved method.
The plastic
concrete removed in front of or behind the paver shall be tested
with an agency-approved air pressure meter in accordance with AASHTO
T-152, Air Content of Freshly Mixed Concrete by the Pressure
Method.(19) The number of pressure meter tests per
sampling location (replicate specimens), and the number of sampling
locations per sublot, shall be defined by the agency in accordance
with the guidelines set forth in chapter 5 of this volume.
- Linear
Traverse Tests of Hardened Concrete Cores. Core specimens
shall be extracted from the hardened concrete slab at predetermined
random sampling locations. Random sampling core locations shall be
determined in accordance with the guidelines set forth in chapter 5 of this volume. Core specimens shall be
extracted between 48 and 72 hours after placement, in accordance
with AASHTO T-24, Obtaining and Testing Drilled Cores and Sawed
Beams of Concrete.(19) All cores used for the acceptance
of entrained air content shall have a minimum diameter of 152 mm.
The number of core specimens per sublot shall be defined by the
agency in accordance with the guidelines set forth in chapter 5 of this volume.
Linear traverse
testing shall be performed on each extracted hardened concrete core
specimen in accordance with ASTM C-457, Standard Test Method for
Microscopical Determination of Parameters of the Air-Void System in
Hardened Concrete.(20) Testing may occur at any time
after the extraction of the core specimen. The measured entrained
air content (expressed as a percentage) for each extracted core is
used as the representative entrained air content value for that
sampling location.
- Entrained Air
Content Acceptance. The contractor shall furnish paving
equipment and employ methods that give the contractor the ability to
produce entrained air contents that meet, or better, the
agency-defined target entrained air content quality. The
agency-desired target entrained air content quality is defined as the
mean and standard deviation of the representative entrained air
content values computed for a given lot. Representative entrained air
content values are determined for each sample location within each
sublot (average of replicates within a sampling location). The
agency-defined target entrained air content shall be defined in table PRS-501-01 of these
specifications. An as-constructed lot with an entrained air content
quality that differs from the target entrained air content quality
shall be accepted with price adjustments (incentive or
disincentive).
The agency shall define AQC limits (RQL and MQL)
to be applied to each specimen value within a sublot. Note: Replicate
specimens may exist at a sampling location if entrained air content is
measured with a pressure meter. The following procedure shall apply:
- If a specimen entrained air content value is less than the
defined RQL, the agency shall begin retesting procedures. Entrained
air content retesting procedures are specified in section PRS–501.05,
Methods of AQC Retesting.
- If a specimen entrained air content value is greater than the
defined MQL, the measured specimen entrained air content value shall
be reduced to be equal to the chosen MQL. The reduced specimen
entrained air content value shall be used for acceptance.
- All specimen entrained air content values greater than or equal
to the RQL, and less than or equal to the MQL, shall be used
directly for acceptance.
If entrained air content is
measured using an air pressure meter, replicate samples shall be
averaged to give representative entrained air content values at
each sample location. If entrained air content is measured using
linear traverse, the representative values are the entrained air
content values measured from each core directly. Regardless of the
sample type chosen, the representative values are used in the PaveSpec
2.0 computer software for the acceptance of entrained air content.
- Initial Smoothness
- Sampling and
Testing of Initial Smoothness. The initial smoothness of the
pavement shall be quantified in terms of a profile index (PI), which
will be determined using a California-type profilograph. The
profilogram is to be recorded on a scale of 2.54 cm or full-scale,
vertically. Motive power may be manual or by propulsion unit attached
to the assembly. The profilograph shall be moved longitudinally along
the pavement at a speed no greater than 4.8 km/h to minimize bounce.
The results of the profilograph test will be evaluated as outlined in
the California Department of Transportation (Caltrans) specification
CA-526. All profile indices are to be determined using a 0.0- or
5.1-mm blanking band.
A minimum of two pavement profiles (one
in each wheelpath) shall be determined for each lane within each
defined sublot. The total number of required pavement profiles per
sublot shall be defined by the agency in accordance with the
guidelines set forth in chapter 5 of this volume. The location of a
wheelpath shall be 0.92 m from a longitudinal joint or
longitudinal pavement edge and parallel to the centerline of the
mainline paving. For widened slabs, the outer wheelpath shall be 0.92
m from the pavement edge paint stripe, rather than the outer pavement
edge. Each profile shall terminate 4.5 m from each bridge approach
pavement or existing pavement that is joined by the new pavement. The
PI determined for each profile shall be converted to a standard unit
of mm/km.
During the initial paving operations, or after a
long shutdown period, the pavement surface shall be tested with the
profilograph when the concrete has cured sufficiently to allow
testing. Membrane curing damaged during the testing operation shall be
repaired by the contractor and at the contractor's expense. If the
initial pavement smoothness, paving methods, and paving equipment are
acceptable, paving operations may proceed.; After initial testing,
profiles of each day's paving will be run prior to continuing paving
operations.
If an average PI of _____ mm/km (limit to be
inserted by the agency) is exceeded in any daily paving operation, the
paving operation will be suspended and not resume until corrective
action is taken.
Within each sublot, all areas represented by
high points having deviations in excess of _____ mm (limit to be
inserted by the agency—10 mm is recommended) in 7.6 m or less shall be
corrected at the contractor's expense. Corrections shall be made using
an approved profiling device or by removing and replacing the
pavement, as directed by the engineer. Bush hammers or other impact
devices shall not be used. Where corrections are made, the surface
texture shall be re-established to provide a uniform texture equal to
the surrounding uncorrected pavement by the contractor and at the
contractor's expense. Corrective work shall be completed prior to
determining pavement thickness.
- Initial Smoothness
Acceptance. The contractor shall furnish paving equipment and
employ methods that give the contractor the ability to produce a
riding surface that meets, or betters, the agency-defined target
initial smoothness quality. The agency-desired target initial
smoothness quality is defined as the mean and standard deviation of
the representative profile indices computed for a given lot.
Representative PI values are determined for each sample location
within each sublot (average of replicates within a sampling location).
The agency-defined target initial smoothness shall be defined in table PRS-501-01 of these specifications. An
as-constructed lot with an initial smoothness quality that differs
from the target smoothness quality shall be accepted with price
adjustments (incentive or disincentive).
The agency shall
define AQC limits (RQL and MQL) to be applied to each specimen PI
value within a sublot. For PI, the RQL will be greater than the MQL
due to the nature of the measurement (the lower the PI, the better the
quality). The following procedures shall apply:
- If a specimen PI value is greater than the defined RQL, the
agency shall begin retesting procedures. Initial smoothness
retesting procedures are specified in section PRS–501.05,
Methods of AQC Retesting.
- If a specimen PI value is less than the defined MQL, the
measured specimen PI value shall be increased to be equal to the
chosen MQL. The increased specimen PI value shall be used for
acceptance.
- All specimen PI values less than or equal to the RQL, and
greater than or equal to the MQL, shall be used directly for
acceptance.
The specimen PI values (including any
adjustments) are then averaged within each profile location to give PI
values representative of each profile sampling location. These PI
values (averages of replicate profile indices) are then used in the
PaveSpec 2.0 computer software for the acceptance of initial
smoothness. The initial smoothness value, typically referred to as a
sample per sublot, is actually the average value of all of the
replicate specimen values at that particular profile
location.
Price adjustments (if any) are based on the as-placed
pavement before any retesting or corrective actions are completed.
- Percent
Consolidation Around Dowels
- Sampling
and Testing of Percent Consolidation Around Dowels. The
percent consolidation around dowels representing the as-constructed
pavement shall be determined within each sublot using an
agency-approved sampling and testing method. The approved sampling and
testing method shall be defined by the agency in accordance with the
guidelines set forth in chapter 5 of this volume.
The representative
percent consolidation around one randomly selected dowel bar in a
sublot shall be determined based on a comparison of the density of two
selected cores extracted from the hardened concrete slab. Core
specimens shall be extracted from the hardened pavement slab between
48 and 72 hours after placement, in accordance with AASHTO T-24,
Obtaining and Testing Drilled Cores and Sawed Beams of
Concrete.(19) All cores used for the acceptance of
percent consolidation around dowels shall have a minimum diameter of
102 mm.
The first of the two required cores shall be taken
through a predetermined randomly selected dowel bar in a randomly
selected transverse joint (random selection of a dowel shall be
determined in accordance with the guidelines set forth in chapter 5 of this volume). The outside edge of the
core through the randomly selected dowel bar shall not be within 0.6 m
of a defined wheelpath or pavement edge, 10 cm of a predicted vibrator
path, or 5 cm of a transverse joint. The dowel bar piece shall be
separated from the concrete core material by an agency-approved
method. The density of this concrete material shall be measured in a
saturated surface dried condition in accordance with ASTM C-642,
Standard Test Method for Specific Gravity, Absorption, and Voids in
Hardened Concrete and labeled as DEN THROUGH-DOWEL(n)
.(20)
The second of the two required cores shall be
taken at a location along a line passing through the first core
(through the dowel bar) and parallel to the centerline of the pavement
unit. The specific longitudinal location of this second core shall be
assumed to be at midslab of the leave slab (the slab away from the
joint in the direction of traffic) adjacent to the randomly selected
transverse joint. The density of this concrete material shall be
measured in a saturated surface dried condition in accordance with
ASTM C-642, Standard Test Method for Specific Gravity, Absorption,
and Voids in Hardened Concrete and labeled as DEN
MID-SLAB(n) .(20)
The number of samples
per sublot (e.g., pairs of cores) shall be defined by the agency in
accordance with the guidelines set forth in chapter 5 of this volume. The maximum of all of the
midslab core densities measured within the given lot (MAX-DEN
MID-SLAB) shall be determined and assumed to represent the
density of a core with 100-percent consolidation. The representative
percent consolidation for each sampling location (set of cores) is,
therefore, determined by the following equation:
%
Consolidation = (DEN THROUGH-DOWEL(n) / MAX-DEN
MID-SLAB) * 100.
(501-1)
- Acceptance
of Percent Consolidation Around Dowels. The contractor shall
furnish paving equipment and employ methods that give the contractor
the ability to produce a percent consolidation around dowels that
meets, or betters, the agency-defined target percent consolidation
quality. The agency-desired target percent consolidation quality is
defined as the mean and standard deviation of the percent
consolidation values computed for a given lot. The agency-defined
target percent consolidation around dowels shall be defined in table PRS-501-01 of these
specifications. An as-constructed lot with a percent consolidation
quality that differs from the target percent consolidation quality
shall be accepted with price adjustments (incentive or
disincentive).
The agency shall define AQC limits (RQL and MQL)
to be applied to each representative percent consolidation value
within a sublot. (Note: A representative percent consolidation value
is defined as the computed percent consolidation value representative
of one sample location.) The following procedures shall apply:
- If a representative percent consolidation sample value is less
than the defined RQL, the agency shall begin retesting procedures.
Percent consolidation retesting procedures are specified in section
PRS–501.05,
Methods of AQC Retesting.
- If a representative percent consolidation sample value is
greater than the defined MQL, the measured representative sample
value shall be reduced to be equal to the chosen MQL. The reduced
representative percent consolidation sample value shall be used for
acceptance.
- All representative percent consolidation sample values greater
than or equal to the RQL, and less than or equal to the MQL, shall
be used directly for acceptance.
The representative
percent consolidation sample values (including any adjustments) are
then used in the PaveSpec 2.0 computer software for the acceptance of
percent consolidation around dowels.
PRS–501.05 Methods of
AQC Retesting.
Additional sampling and testing for any of the AQC's for acceptance
testing may be requested at any time by the contractor or by the agency.
The agency shall conduct all of the sampling and testing for any retesting
activities.
The following specific conditions shall be applied for
determining whether the agency or contractor is responsible for the cost
of the retesting:
Insert agency-defined conditions used to define
retesting cost responsibility.
The pavement shall be retested only once in accordance with the
retesting methods described in this section. Retesting procedures shall be
initiated when any measured AQC specimen value fails to meet or exceed the
respective agency-defined RQL. The purpose of retesting is to determine if
the AQC quality provided by the contractor is truly less than the quality
defined by the RQL.
If retesting procedures determine conclusively
that an identified area of pavement is deficient in quality (having lesser
quality than the respective agency-defined RQL), the result shall be the
removal and replacement of the identified area. AQC sampling and testing
values from the replaced material shall then be used in place of the
original sampling and testing results for that sampling location. However,
the measured AQC samples are subjected to MQL's equal to the respective
AQC target values (i.e., the contractor may not get credit for AQC quality
better than the target values when material has been removed and
replaced).
If retesting procedures determine conclusively that an
identified area of pavement is not deficient in quality (having greater
quality than the respective agency-defined RQL), the additional AQC
samples taken for retesting shall be added to the original AQC sample
value set (if no testing error occurred). The average of all the AQC
sampling and testing results (original and retesting) representing a
sampling location shall then be used as the representative AQC value for
that sampling location.
The retesting procedures for each AQC are
described separately below.
- Concrete Strength.
If a concrete strength specimen sample is found to be less than the
agency-defined concrete strength RQL, the following procedure shall
apply:
Insert agency-defined concrete strength retesting
procedures here.
- Slab Thickness. If a
slab thickness specimen sample is found to be less than the
agency-defined slab thickness RQL, the following procedure shall
apply:
Insert agency-defined slab thickness retesting
procedures here.
- Entrained Air
Content. If an entrained air content specimen sample is found to
be less than the agency-defined entrained air content RQL, the following
procedure shall apply:
Insert agency-defined entrained air content
retesting procedures here.
- Initial Smoothness.
If an initial PI specimen sample is found to be less than the
agency-defined initial PI RQL, the following procedure shall apply:
Insert agency-defined initial smoothness retesting
procedures here.
- Percent
Consolidation Around Dowels If a percent consolidation around
dowels specimen sample is found to be less than the agency-defined
percent consolidation RQL, the following procedure shall apply:
Insert agency-defined percent consolidation around
dowels retesting procedures here.
PRS–501.06 Basis of
Acceptance
- Life-Cycle Costs. The
agency-chosen AQC's are combined into a single characteristic
representing the pavement quality, the post-construction LCC of the
pavement expected to be incurred over the designated analysis period.
The post-construction LCC quality characteristic relates directly to the
future performance of the pavement. The post-construction LCC shall be
used as the single overall characteristic representing a pavement lot's
quality for acceptance.
- As-Designed Target
Pavement. The target as-designed pavement is defined as the
desired construction quality for which the agency will pay 100 percent
of the contractor bid price. It includes target means and standard
deviations for each of the AQC's considered in the agency-chosen
acceptance plan. The target AQC standard deviations are representative
of acceptable AQC variability. These standard deviations are
point-to-point variations (including materials and testing variations)
for concrete strength, slab thickness, and entrained air content in the
slab; variations between longitudinal profiles for initial smoothness;
and dowel-to-dowel variations for percent consolidation of
concrete.
The as-designed target lot mean LCC (LCC DES
) is determined by simulating an agency-defined number of lots with the
AQC means and standard deviations set at the agency-defined target
values. (The number of lots used for the simulation shall be defined by
the agency in accordance with the guidelines set forth in chapter 5 of this volume.) This simulation of LCC
DES shall be accomplished using the PaveSpec 2.0 computer
software. The project-specific constant values required for the
simulation of LCC's shall be defined by the agency and included as Series
C attachments to these specifications. Appropriate values for
the constant values shall be selected by the agency in accordance with
the guidelines set forth in chapter 5 of this volume. The agency-defined AQC target
values (means and standard deviations), and the respective acceptance
sampling and testing procedures, are defined in table
PRS-501-01.
- As-Constructed
Pavement Lot. The acceptance of the as-constructed pavement lot
is based on the representative AQC testing values measured in accordance
with the agency-defined sampling and testing plan summarized in table
PRS-501-01. The AQC representative sample values are summarized
differently according to the chosen pay adjustment
method.
PRS–501.07 Basis of
Payment
The agency shall determine contractor pay adjustments using Level 1 or
Level 2 pay adjustment methods. The specific procedures for each are
described below.
- Level 1 Pay
Adjustment. [Recommended for initial implementation of PRS.]
- Simulation of the Target As-Designed Lot LCC. Prior to the
placement of any mainline PCC, the agency must determine the one LCC
value representing the target as-designed LCC (LCC DES ).
This LCC DES is determined from simulation procedures
(using the PaveSpec 2.0 computer software) and is based on the
agency-defined AQC target values (summarized in table PRS-501-01). The LCC
DES shall be used as the one overall characteristic
representing the quality of the as-designed target pavement.
- Development of Individual AQC Pay Factor Charts and
Equations. Prior to the placement of any mainline PCC, individual
pay factor charts (and respective equations) shall be developed for
each of the AQC's selected by the agency for inclusion in the
specification (see section PRS–501.04,
Method of Measurement, Definition of Pavement Performance).
These individual AQC pay factor charts and equations are based on the
LCC DES simulated in step 1 and shall be developed using
the PaveSpec 2.0 computer software. The required pay factor charts and
equations shall be included as Series
D attachments to these specifications.
- Development of a Lot Composite Pay Factor Equation. Prior
to the placement of any mainline PCC, an appropriate lot composite pay
factor (CPF) equation shall be determined by the agency in accordance
with the guidelines set forth in chapter 6 of this volume. Only those AQC's chosen by
the agency for acceptance shall be considered in the CPF
equation.
- Summary of Representative Lot AQC Sample Values. When using
the Level 1 pay adjustment procedure, all of the representative sample
values shall be statistically summarized into representative AQC lot
means and standard deviations. (Note: If more than one sample is taken
from a single sampling location, the mean of the replicate samples is
used as the representative sample value for that location.) These
computed AQC lot means and standard deviations are used to define the
quality of the as-constructed lot and shall be used as the basis of
computed pay adjustments. Specific definitions of sample means and
sample standard deviations are contained in the list of definitions
included in section PRS–101
of this specification.
- Determination of Individual AQC Lot Pay Factors. Individual
lot pay factors shall be determined (for each AQC chosen for
acceptance) based on the computed AQC lot means and standard
deviations. Individual lot AQC pay factors are determined using the
computed lot AQC means and standard deviations in the individual AQC
pay factor curves and equations (included as Series
D attachments to these specifications). Individual AQC pay
factor calculations shall be completed in accordance with the
procedure set forth in chapter 8 of this volume.
If the agency chooses
to apply pay factor limits to any or all of the individual AQC lot pay
factors, they must be selected and applied in accordance with the
guidelines set forth in chapter
6 of this volume.
- Calculation of the Overall Lot CPF. The CPF for the
as-constructed lot shall be computed using the agency-defined CPF
equation. The resulting composite lot pay factor (PF
COMPOSITE ) shall be used to determine the actual
contractor pay adjustment. If the agency chooses to apply limits
(minimum or maximum) to the overall lot CPF, the following shall apply
[the agency shall insert appropriate values into the provided
blanks]:
- If PF COMPOSITE is determined to be less than ______
percent, the agency shall make a determination if the work can
remain in place. If allowed to remain in place, the agency shall
accept the non-specification work using an adjusted CPF of PF
COMPOSITE = ______ percent.
- If PF COMPOSITE is determined to be greater than
______ percent, the agency shall accept the lot using an adjusted
CPF of PF COMPOSITE = ______ percent.
Agency-chosen limits to the overall composite lot pay factor
shall be applied in accordance with the guidelines set forth in chapter
6 of this volume.
- Adjustment of Contractor Bid Price. The total payment to
the contractor for the as-constructed lot shall be determined using
the following equation:
PAY LOT = BID * (PF COMPOSITE
/ 100) * LOT LENGTH
(501-02)
where
PAY LOT = Adjusted payment paid to the
contractor for the as-constructed lot, $.
BID =
Contractor bid price, $/km.
PF COMPOSITE =
The determined Level 1 lot CPF, percent (e.g., 101 percent is
expressed as 101.0).
LOT LENGTH = Measured
actual as-constructed lot length, km.
- Level 2 Pay
Adjustment
- Simulation of the Target As-Designed Lot LCC. Prior to the
placement of any mainline PCC, the agency must determine the one LCC
value representing the target as-designed LCC (LCC DES ).
This LCC DES is determined from simulation procedures
(using the PaveSpec 2.0 computer software) and is based on the
agency-defined AQC target values (summarized in table
PRS-501-01). The LCC DES shall be used as the one
overall characteristic representing the quality of the as-designed
target pavement.
- Summary of Representative Sublot AQC Sample Values. When
using the Level 2 pay adjustment procedure, all of the representative
sample values (representing each sampling location—including adjusted
sample values) within each sublot shall be statistically summarized
into specific sublot means for each AQC. (Note: These values are
computed in the PaveSpec 2.0 computer software.) These computed AQC
sublot means are used to define the quality of each respective
as-constructed sublot and shall be used as the basis for computed pay
adjustments for the as-constructed lot.
- Simulation of the As-Constructed Lot LCC. The computed AQC
sublot means are used to simulate the one LCC used to represent the
actual as-constructed lot (LCC CON ). The respective LCC
CON shall be computed using the PaveSpec 2.0 computer
software. The LCC CON shall be used as the one overall
characteristic representing the quality of the actual as-constructed
pavement.
- Calculation of the Overall Lot Pay Factor.The overall lot
pay factor for the as-constructed lot shall be computed using the
following equation:
PF LOT = 100 * (BID + [LCC
DES – LCC CON ]) / BID
(501-03) where
PF LOT = Overall pay factor for the
as-constructed lot, percent.
BID = Contractor bid price, $/km.
LCC DES = Simulated representative
as-designed target lot LCC (based on target AQC lot means and
standard deviations), $/km.
LCC CON = Simulated representative
as-constructed lot LCC (based on measured AQC sublot means),
$/km.
The resulting overall lot pay factor (PF LOT ) shall be
used to determine the actual contractor pay adjustment. If the
agency chooses to apply limits (minimum or maximum) to the overall lot
pay factor, the following shall apply (Note: The agency shall
insert appropriate values into the provided blanks.):
- If PF LOT is determined to be less than ______
percent, the agency will make a determination if the work can remain
in place. If allowed to remain in place, the agency shall
accept the non-specification work using an adjusted lot pay factor
of PF LOT = ______ percent.
- If PF LOT is determined to be greater than ______
percent, the agency shall accept the lot using an adjusted lot pay
factor of PF LOT = ______ percent.
Agency-chosen limits to the overall lot pay factor shall be applied
in accordance with the guidelines outlined in chapter
6 of this volume.
- Adjustment of Contractor Bid Price. The total payment
to the contractor for the as-constructed lot may be determined by one
of the following equations:
PAY LOT = (LCC DES – LCC
CON ) * LOT LENGTH
(501-04)
or
PAY LOT = BID * (PF LOT / 100) *
LOT LENGTH
(501-05)
where
PAY LOT = Adjusted payment paid to the
contractor for the as-constructed lot, $.
LCC DES = Simulated representative
as-designed target lot LCC (based on target AQC lot means and standard
deviations), PW$/km.
LCC DES = Simulated representative
as-constructed lot LCC (based on measured AQC sublot means),
PW$/km.
BID = Contractor bid price, $/km.
PF LOT = The determined Level 2 overall pay
factor for the as-constructed lot, percent (e.g., 101 percent is
expressed as 101.0).
LOT LENGTH = Measured actual as-constructed
lot length, km.
Attachment Series A—Laboratory
Maturity Calibration Curves and Respective
Equations |
 |
 |
Attachment Series A may contain any or all of the following
laboratory-developed concrete strength versus maturity curves (as so
required by section PRS–501.04–G.1.c.i,
Laboratory Maturity Calibration of these PRS specifications):
- Flexural strength (third-point loading) versus maturity.
- Compressive strength versus maturity.
- Split-tensile strength (third-point loading) versus
maturity.
Each required curve is developed using the Arrhenius maturity method.
The resulting strength versus maturity regression equations, determined in
accordance with the guidelines set forth in chapter 5 of this volume, are presented in table PRS–A–1.
(if applicable, insert flexural strength
(third-point loading) versus maturity chart
here) |
Figure PRS–A–1.
Laboratory-developed flexural strength (third-point loading) versus
maturity chart.
(if applicable, insert compressive strength
versus maturity chart here) |
Figure PRS–A–2.
Laboratory-developed compressive strength versus maturity
chart.
(if applicable, insert split-tensile strength
versus maturity chart here) |
Figure PRS–A–3.
Laboratory-developed split-tensile strength versus maturity
chart.
Table
PRS–A–1. Strength versus maturity regression equations (if
applicable).
Maturity Curve |
Regression Equation1 |
Flexural Strength (third-point
loading)2 |
MR = f(AMAT) |
Compressive Strength3 |
f’c = f(AMAT) |
Split-Tensile Strength4 |
ST = f(AMAT) |
1Regression equations are functions of Arrhenius maturity
(AMAT), expressed as an Equivalent Age (hours).
2 Flexural (third-point loading) strengths are expressed as
MR.
3 Compressive strengths are expressed as f’c.
4 Split-tensile strengths are expressed as ST.
Attachment Series
B–Laboratory-Developed Inter-Strength Curves and
Respective Equations |
 |
 |
Attachment Series B may contain one or both of the following
laboratory-developed inter-strength relationship curves (as so required by
section PRS–501.04–G.1.c.ii,
Laboratory-Developed Inter-Strength Relationships of these
specifications):
- Compressive strength versus flexural strength (third-point
loading).
- Split-tensile strength versus flexural strength (third-point
loading).
Inter-strength relationships are determined by conducting different
strength testing on specimens at the same equivalent maturities. The
resulting equations giving the relationships between 28-day (equivalent
laboratory maturity) compressive or split-tensile strength and 28-day
flexural strength (third-point loading), determined in accordance with the
guidelines set forth in chapter 5 of this volume, are presented in table
PRS–B–1.
(if applicable, insert compressive versus
flexural strength [third-point loading] inter-strength chart
here) |
Figure PRS–B–1.
Laboratory-developed compressive strength versus flexural strength
(third-point loading) chart. Each point on the chart represents a
comparison of strengths at equivalent maturities.
(if applicable, insert split-tensile versus
flexural strength [third-point loading] inter-strength chart
here) |
Figure PRS–B–2.
Laboratory-developed split-tensile strength versus flexural strength
(third-point loading) chart. Each point on the chart represents a
comparison of strengths at equivalent maturities.
Table
PRS–B–1. Inter-strength relationships at an equivalent laboratory maturity
of 28 days (if applicable).
28-day Inter-Strength Relationship |
Equation |
Compressive1 to Flexural
Strength3 |
28-day MR = f(28-day f’c) |
Split-Tensile2 to Flexural
Strength3 |
28-day MR = f(28-day
ST) |
1Compressive strengths at an equivalent laboratory maturity
of 28 days are expressed as 28-day f’c.
2Split-tensile strengths at an equivalent laboratory
maturity of 28 days are expressed as 28-day ST.
3 Flexural (third-point loading) strengths at an equivalent
laboratory maturity of 28 days are expressed as 28-day
MR.
Attachment Series C–Project-Specific Constant
Values |
 |
 |
Attachment Series C consists of a table containing all of the
project-specific constant values required to define the as-designed and
as-constructed pavements (as stated in section PRS–501.06–B,
As-Designed Target Pavement of these specifications).
Table
PRS–C–1. Table of project-specific constant values.
(insert table of project-specific constant values
here) |
Attachment Series D–Level 1 Individual AQC Pay
Factor Charts and Equations |
 |
 |
Attachment Series D shall contain individual pay factor charts
(and respective pay factor equations) for all of the AQC’s chosen for
inclusion in these specifications under section PRS–501.04–D,
Included Acceptance Quality Characteristics. Each AQC pay
factor chart is developed in accordance with the guidelines set forth in
chapter 7 of this volume. The resulting pay factor
regression equations (developed for specific agency-selected AQC standard
deviations in accordance with chapter 7 of this volume) are presented in table
PRS–D–1.
(if applicable, insert Level 1 concrete strength
pay factor chart here) |
Figure PRS–D–1. Level 1
concrete strength pay factor chart.
(if applicable, insert Level 1 slab thickness pay
factor chart here) |
Figure PRS–D–2. Level 1
slab thickness pay factor chart.
(if applicable, insert Level 1 entrained air
content pay factor chart here) |
Figure PRS–D–3. Level 1
entrained air content pay factor chart.
(if applicable, insert Level 1 initial smoothness
pay factor chart here) |
Figure PRS–D–4. Level 1
initial smoothness pay factor chart.
(if applicable, insert Level 1 percent
consolidation around dowels pay factor chart
here) |
Figure PRS–D–5. Level 1
percent consolidation around dowels pay factor chart.
Table
PRS–D–1. Level 1 AQC pay factor regression equations (if
applicable).
Acceptance Quality Characteristic |
As-Constructed Standard Deviation
(s)1 |
Pay-Factor Regression Equation2 |
Concrete Strength |
STR–s1 |
PFSTR(1) = f(strength
mean) |
· |
· |
· |
· |
· |
· |
STR–si |
PFSTR(i) = f(strength
mean) |
Slab Thickness |
THK–s1 |
PFTHK(1) = f(slab thickness mean)
|
· |
· |
· |
· |
· |
· |
THK–sj |
PFTHK(j) = f(slab thickness
mean) |
Entrained Air Content |
AIR–s1 |
PFAIR(1) = f(entrained air content
mean) |
· |
· |
· |
· |
· |
· |
AIR–sk |
PFAIR(k) = f(entrained air content
mean) |
Initial Smoothness |
SM–s1 |
PFSM(1) = f(initial smoothness
mean) |
· |
· |
· |
· |
· |
· |
SM–sl |
PFSM(l) = f(initial smoothness
mean) |
Percent Consolidation Around Dowels |
CON–s1 |
PFCON(1) = f(percent consolidation
mean) |
· |
· |
· |
· |
· |
· |
CON–sm |
PFCON(m) = f(percent consolidation
mean) | 1Specific standard deviations are chosen by the agency.
Regression equations are typically developed for three to five different
agency-chosen standard deviations for each AQC.
2Regression equations are
functions of the respective AQC measured mean.
References |
 |
 |
- Darter, M.I., M. Abdelrahman, P.A. Okamoto, and K.D. Smith.
Performance-Related Specifications for Concrete Pavements: Volume
I—Development of a Prototype Performance-Related Specification.
FHWA-RD-93-042. Washington, DC: Federal Highway Administration,
1993.
- Darter, M.I., M. Abdelrahman, T. Hoerner, M. Phillips, K.D. Smith,
and P.A. Okamoto. Performance-Related Specifications for Concrete
Pavements: Volume II—Appendix A, B, and C. FHWA-RD-93-043.
Washington, DC: Federal Highway Administration, 1993.
- Okamoto, P.A., C.L. Wu, S.M. Tarr, M.I. Darter, and K.D. Smith.
Performance-Related Specifications for Concrete Pavements: Volume
III—Appendix D and E. FHWA-RD-93-044. Washington, DC: Federal
Highway Administration, 1993.
- Glossary of Highway Quality Assurance Terms. Transportation
Research Circular 457. Washington, DC: National Academy Press,
1996.
- Performance-Related Specifications (PRS): A Cooperative Effort to
Improve Pavement Quality. FHWA-SA-97-008. Washington, DC: Federal
Highway Administration, 1997.
- Afferton, K.C., J. Freidenrich, and R.M. Weed. "Managing Quality:
Time for a National Policy." Transportation Research Record 1340.
Washington, DC: National Academy Press, 1996, pp. 3-39.
- Weed, R.M. Statistical Specification Development.
FHWA/NJ-88-017. Trenton: New Jersey Department of Transportation,
1989.
- Darter, M.I., T.E. Hoerner, K.D. Smith, P.A. Okamoto, and P.A.
Kopac. "Development of a Prototype Performance-Related Specification for
Concrete Pavements." Transportation Research Record 1544.
Washington, DC: National Academy Press, 1996, pp. 81-90.
- AASHTO Highway Subcommittee on Construction. Quality Assurance
Guide Specification. Washington, DC: American Association of State
Highway and Transportation Officials, 1996.
- "Review of Life-Cycle Costing Analysis Procedures." Interim report
prepared by ERES Consultants, Inc., Brent Rauhut Engineering, Inc., and
the ADI Group for the Ministry of Transportation of Ontario,
1997.
- ERES Consultants, Inc. Techniques for Pavement Rehabilitation:
Participant's Manual. 5th ed. Champaign, IL: ERES,
1993.
- ERES Consultants, Inc. "Long Term Pavement Performance Data
Analysis, Volume III: Design and Construction of PCC Pavements—Improved
PCC Performance Models." Preliminary Draft Final Report prepared for the
Federal Highway Administration, 1997.
- McFarland, W.F. Benefit Analysis for Pavement Design Systems.
Report 123-13. Austin: Texas Highway Department, 1972.
- American Association of State Highway and Transportation Officials.
AASHTO Guide for Design of Pavement Structures. Washington, DC:
AASHTO, 1993.
- Chamberlin, W.P. Performance-Related Specifications for Highway
Construction and Rehabilitation. NCHRP Synthesis 212. Washington,
DC: National Academy Press, 1995.
- Darter, M.I. Design of Zero-Maintenance Plain Jointed Concrete
Pavement, Volume I: Development of Design Procedures.
FHWA-RD-77-111. Washington, DC: Federal Highway Administration,
1977.
- U.S. Army Corps of Engineers. Engineering and Design, Pavement
Design for Frost Conditions. EM-1110-345-306.
- Weed, R.M. Quality Assurance Software for the Personal
Computer. FHWA-SA-96-026. Washington, DC: Federal Highway
Administration, 1996.
- American Association of State Highway and Transportation Officials.
Standard Specifications for Transportation Materials and Methods of
Sampling and Testing, Part II: Tests. 17th ed.
Washington, DC: AASHTO, 1995.
- American Society for Testing and Materials. Annual Book of ASTM
Standards, Volume 04.03: Road and Paving Materials; Pavement Management
Technologies. Philadelphia: ASTM, 1992.
- Smith, K.L., K.D. Smith, L.D. Evans, T.E. Hoerner, M.I. Darter, and
J.H. Woodstrom. "Smoothness Specifications for Pavements." Final report
prepared for the National Cooperative Highway Research Program,
1997.
- Walker, R.S., and H.T. Lin. Profilograph Correlation Study With
Present Serviceability Index (PSI). FHWA-DP-88-072-002. Austin:
Texas State Department of Highways and Public Transportation,
1988.
- Uddin, W., W.R. Hudson, and G. Elkins. "Surface-Smoothness
Evaluation and Specifications for Flexible Pavements." ASTM STP 1031,
Surface Characteristics of Roadways: International Research and
Technologies. Philadelphia: American Society for Testing and
Materials, 1990.
- Kombe, E.M., and S.A. Kalevela. Development and Evaluation of
Initial Pavement Smoothness for Construction Specifications.
FHWA-AZ-SP9201. Arizona Department of Transportation.
- Goulias, D.G., T. Dossey, and W.R. Hudson. End-Result Smoothness
Specifications for Rigid and Flexible Pavements in Texas.
FHWA/TX-93+1167-2F. Austin: Texas State Department of Highways and
Public Transportation, 1992.
- Kulakowski, B.T., and J.C. Wambold. Development of Procedures for
the Calibration of Profilographs. FHWA-RD-89-110. McLean, VA:
Federal Highway Administration, 1989.
- Kleskovic, P.Z. A Discussion of Discount Rates for Economic
Analysis of Pavements. Washington, DC: Federal Highway
Administration, 1990.
- AASHTO Highway Subcommittee on Construction. Implementation
Manual for Quality Assurance. Washington, DC: American Association
of State Highway and Transportation Officials, 1996.
- AASHTO Highway Subcommittee on Construction. Guide Specifications
for Highway Construction. Washington, DC: American Association of
State Highway and Transportation Officials, 1993.
|